Updating end-of-life equipment to enhance resilience and decarbonize
This case study was chosen as part of the Empire Building Challenge competition. Click here to learn more about the Empire Building Challenge competition.
Tags
59-17 Junction Boulevard, developed by LeFrak Commercial, highlights the crucial intersection between decarbonization and resiliency. The 454,645 square foot, 20-story commercial property located in Queens, NY was built in 1970 and features an inefficient 2-pipe heating and cooling system that has reached the end of its useful life, due in part to damage sustained by Hurricane Ida.
As part of their participation in the Empire Building Challenge, LeFrak will complete a significant decarbonization project valued at $19.7 million, resulting in the overall reduction of onsite fossil fuels by 2035. The measures aim to electrify and recover heat of thermal loads at the property, immediately reducing site energy use by over 33% from a 2021 baseline.
LeFrak is a preeminent, family-owned property company that owns and manages an extensive portfolio of real property concentrated in the New York/New Jersey metropolitan area, as well as South Florida, Los Angeles, and throughout the West Coast.
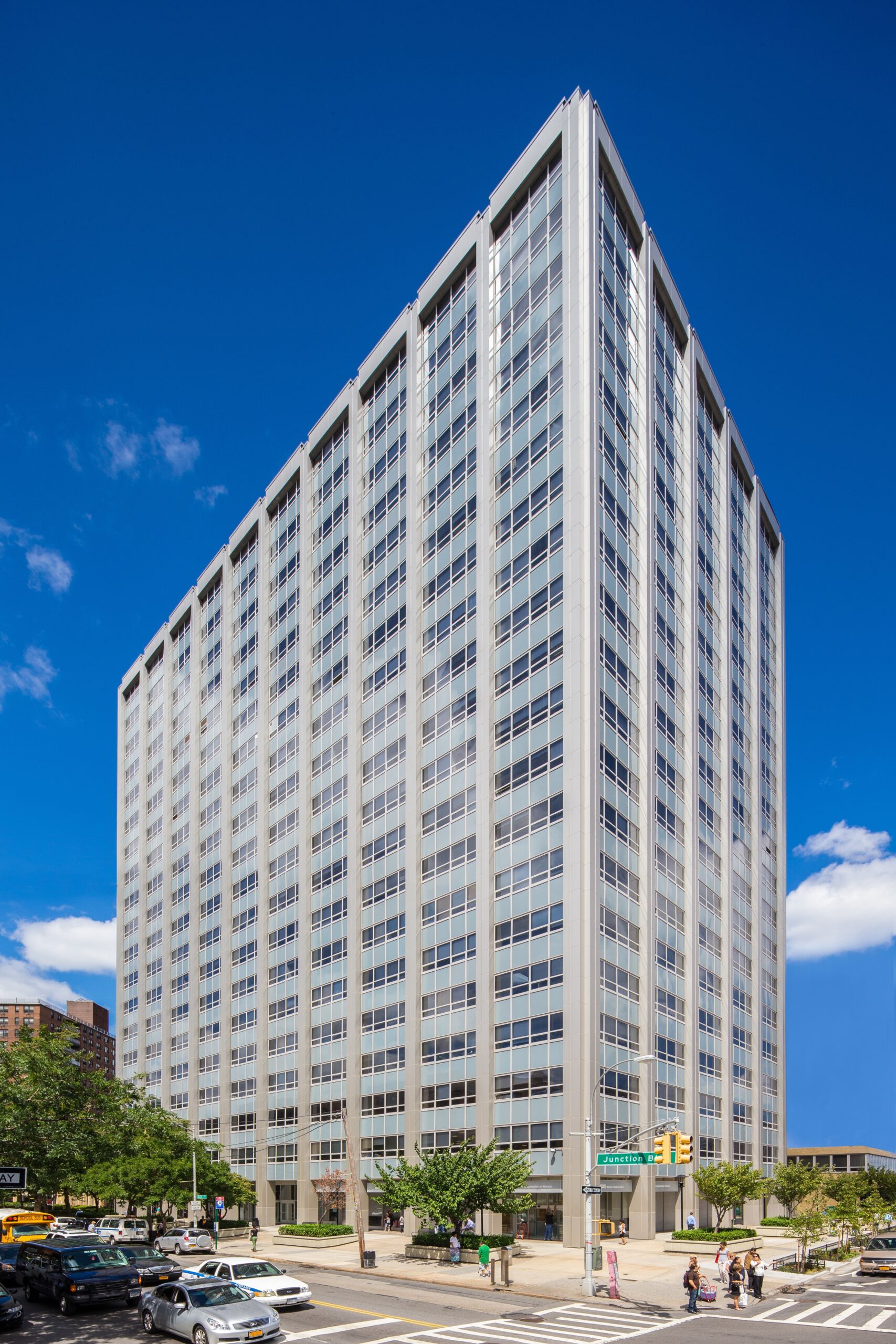
Project Highlights
Step 1
Step 1: Examine Current Conditions
A baseline assessment is key to understanding current systems and performance, then identifying conditions, requirements or events that will trigger a decarbonization effort. The assessment looks across technical systems, asset strategy and sectoral factors.
Building System Conditions
- Equipment nearing end-of-life
- Damage from events
- Resilience upgrades
- Efficiency improvements
Asset Conditions
Market Conditions
The plan for decarbonization was developed with short- and long-term needs in mind and was prompted by heating and cooling equipment that has reached the end of its useful life, due in part to damage sustained by Hurricane Ida. This project highlights the intersection between decarbonization and resiliency, in which necessary upgrades can be leveraged to integrate low-carbon solutions and safeguard critical building systems from future climate impacts. The immediate capital work, slated for 2024-2025, has been structured to facilitate the elimination of on-site fossil fuel consumption by the end of the 2035 decarbonization period, with careful consideration given to constructability, importance of tenant disruption, and financial implications.
Step 2
Step 2: Design Resource Efficient Solutions
Effective engineering integrates measures for reducing energy load, recovering wasted heat, and moving towards partial or full electrification. This increases operational efficiencies, optimizes energy peaks, and avoids oversized heating systems, thus alleviating space constraints and minimizing the cost of retrofits to decarbonize the building over time.
Existing Conditions
This diagram illustrates the building prior to the initiation of Strategic Decarbonization planning by the owners and their teams.
Click through the measures under “Building After” to understand the components of the building’s energy transition.
Sequence of Measures
2024
Building System Affected
- heating
- cooling
- ventilation
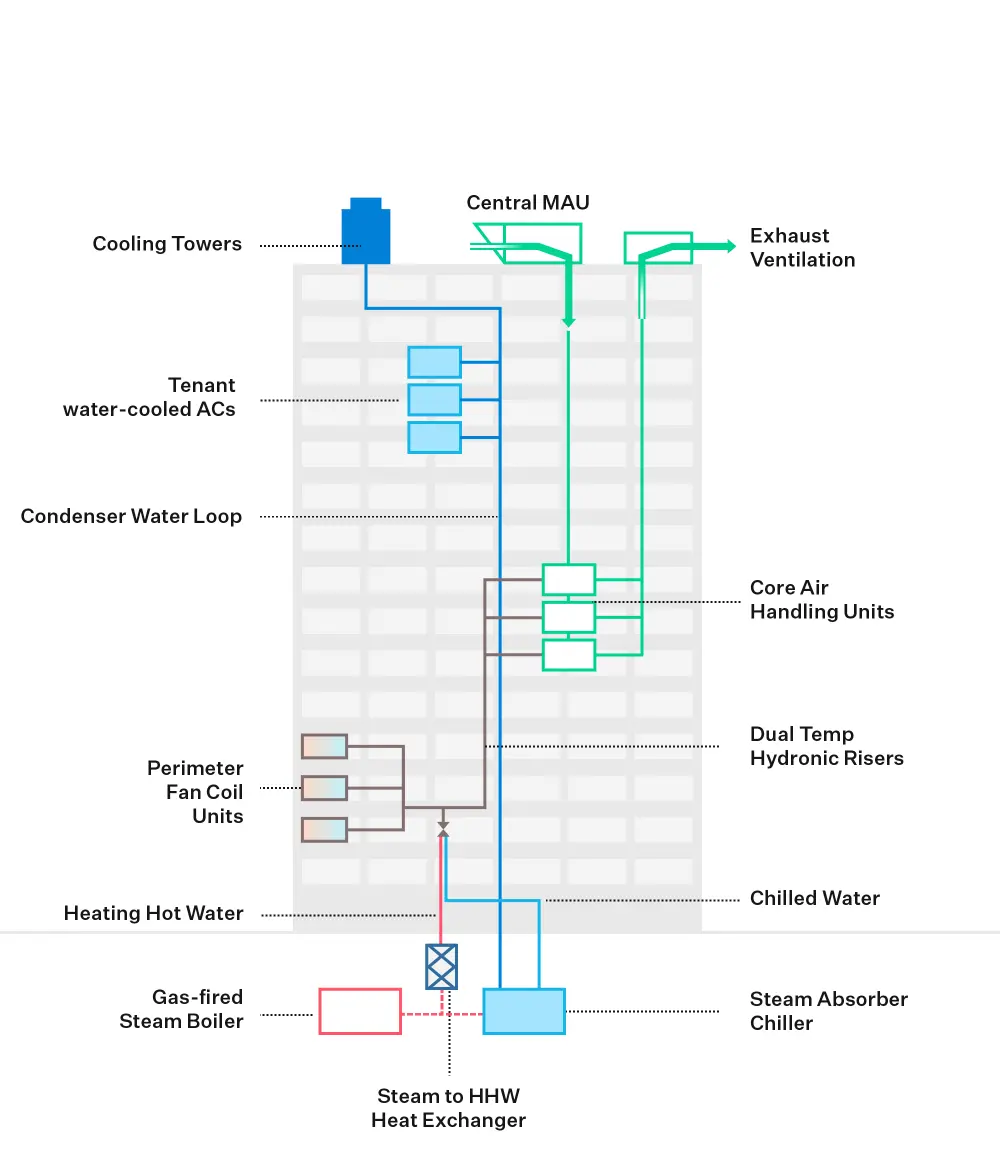
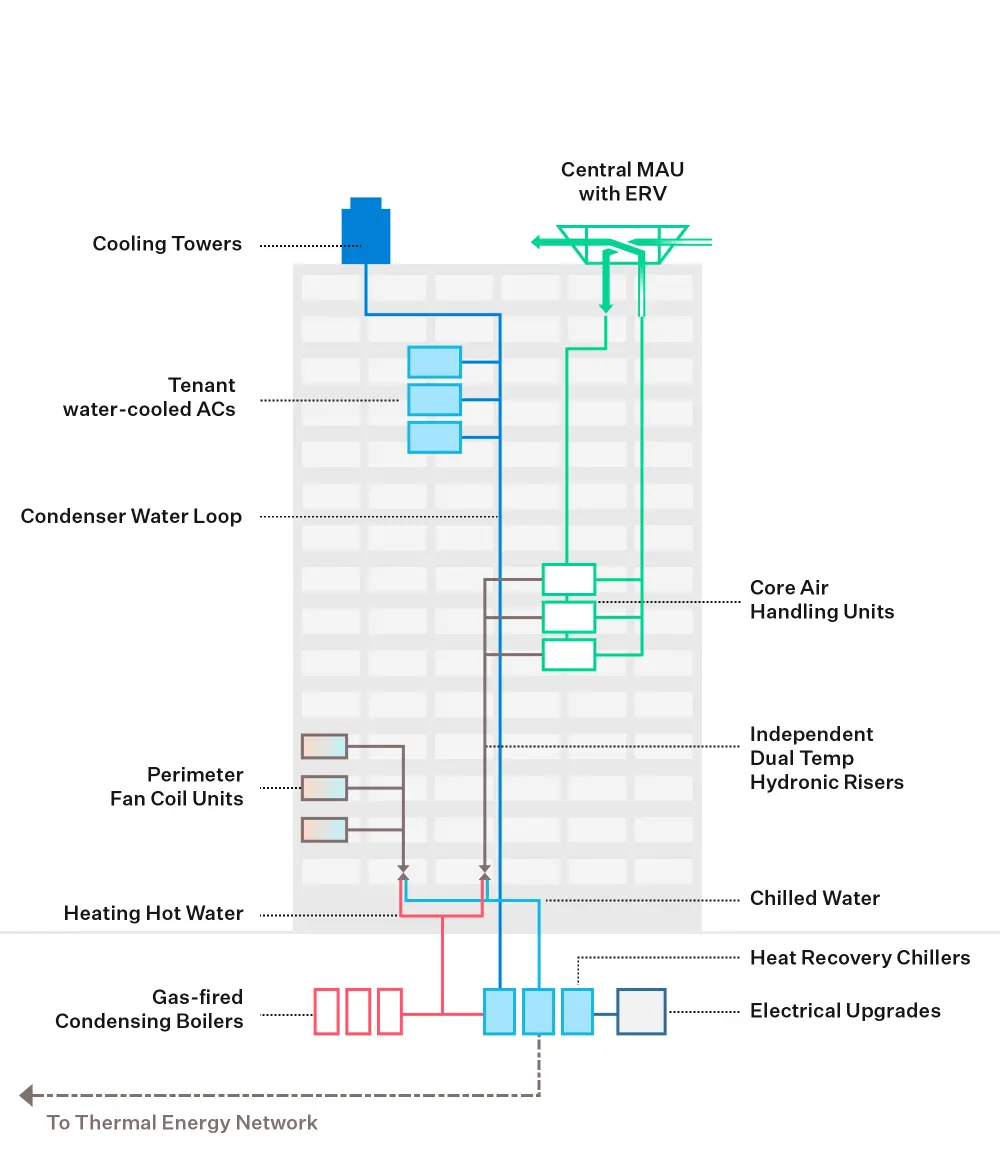
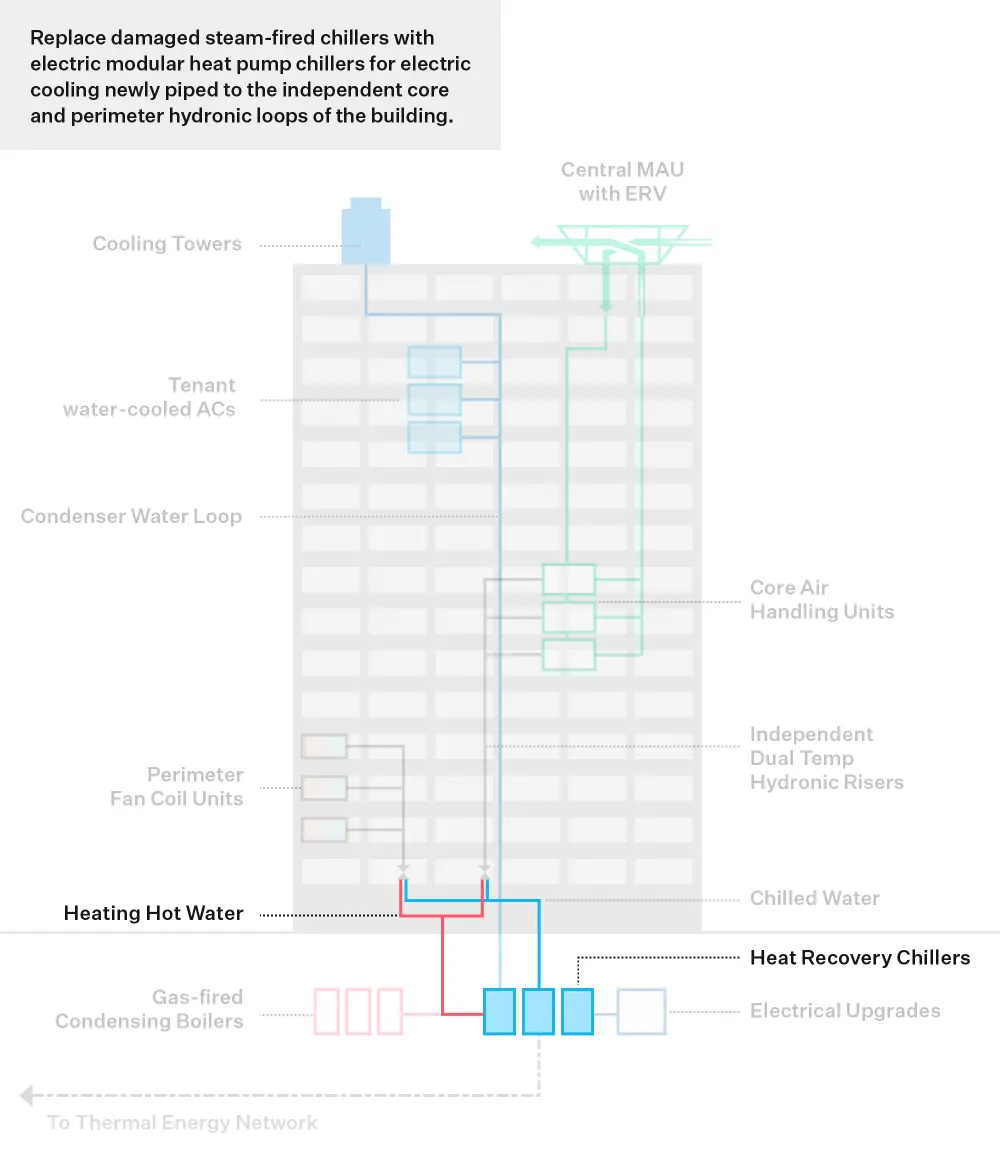
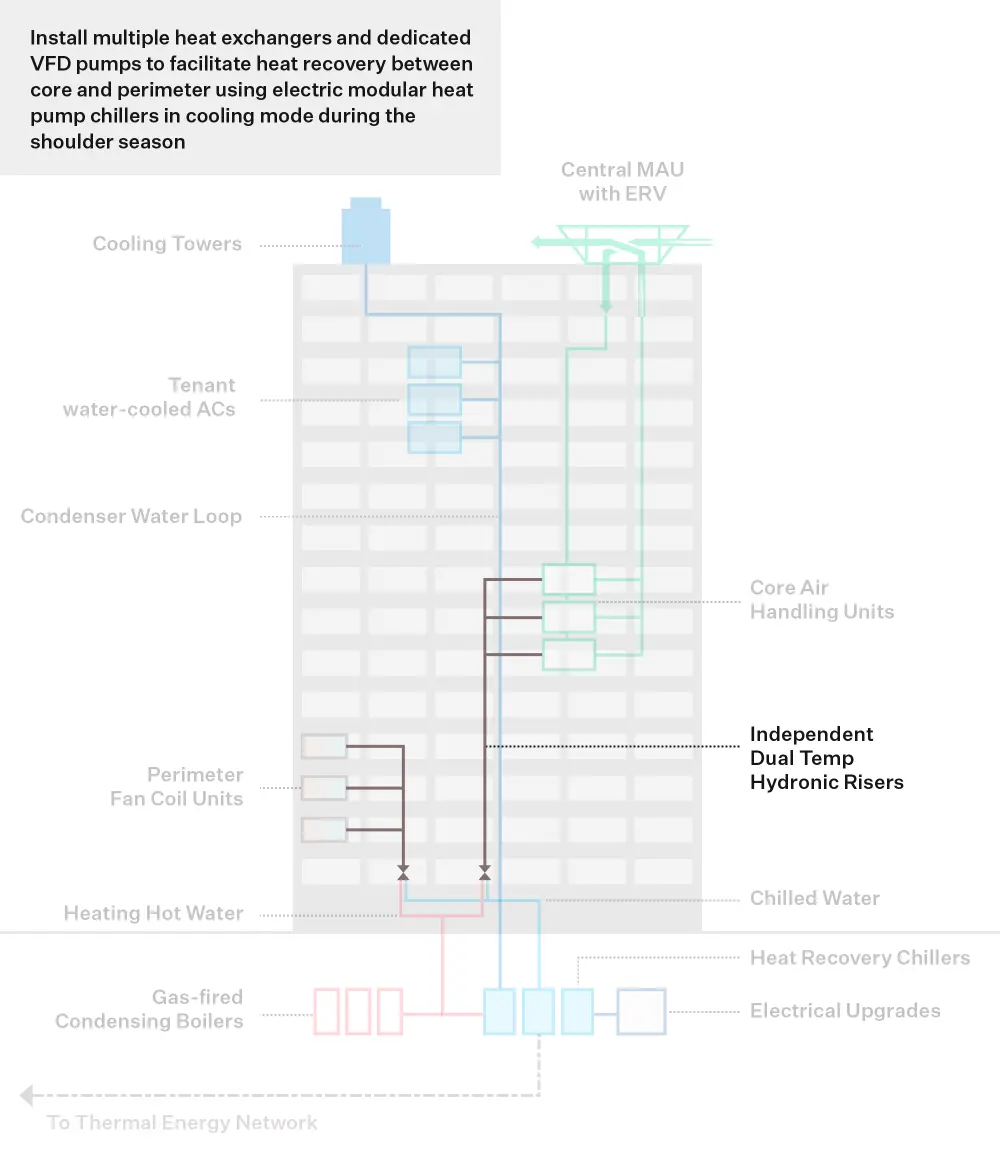
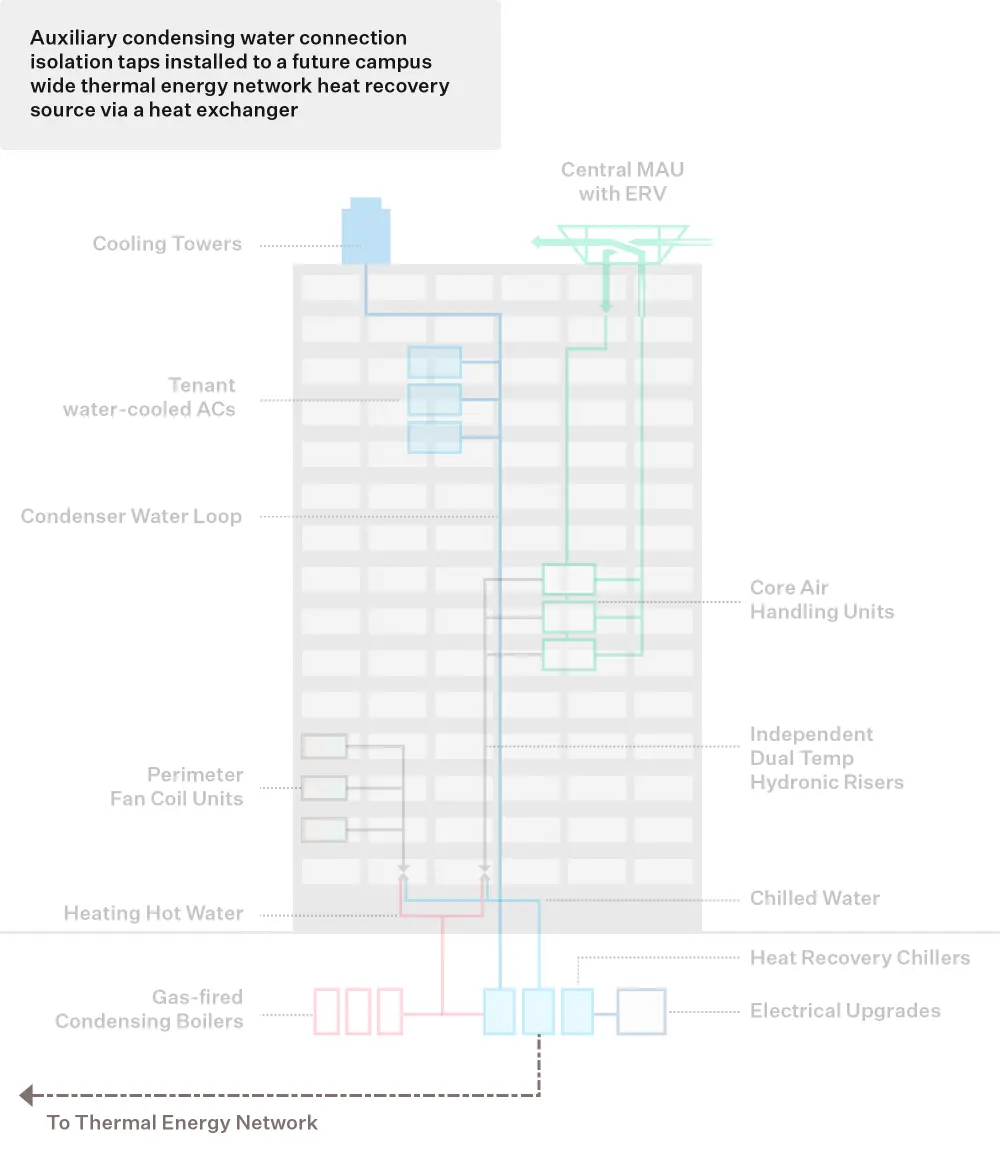
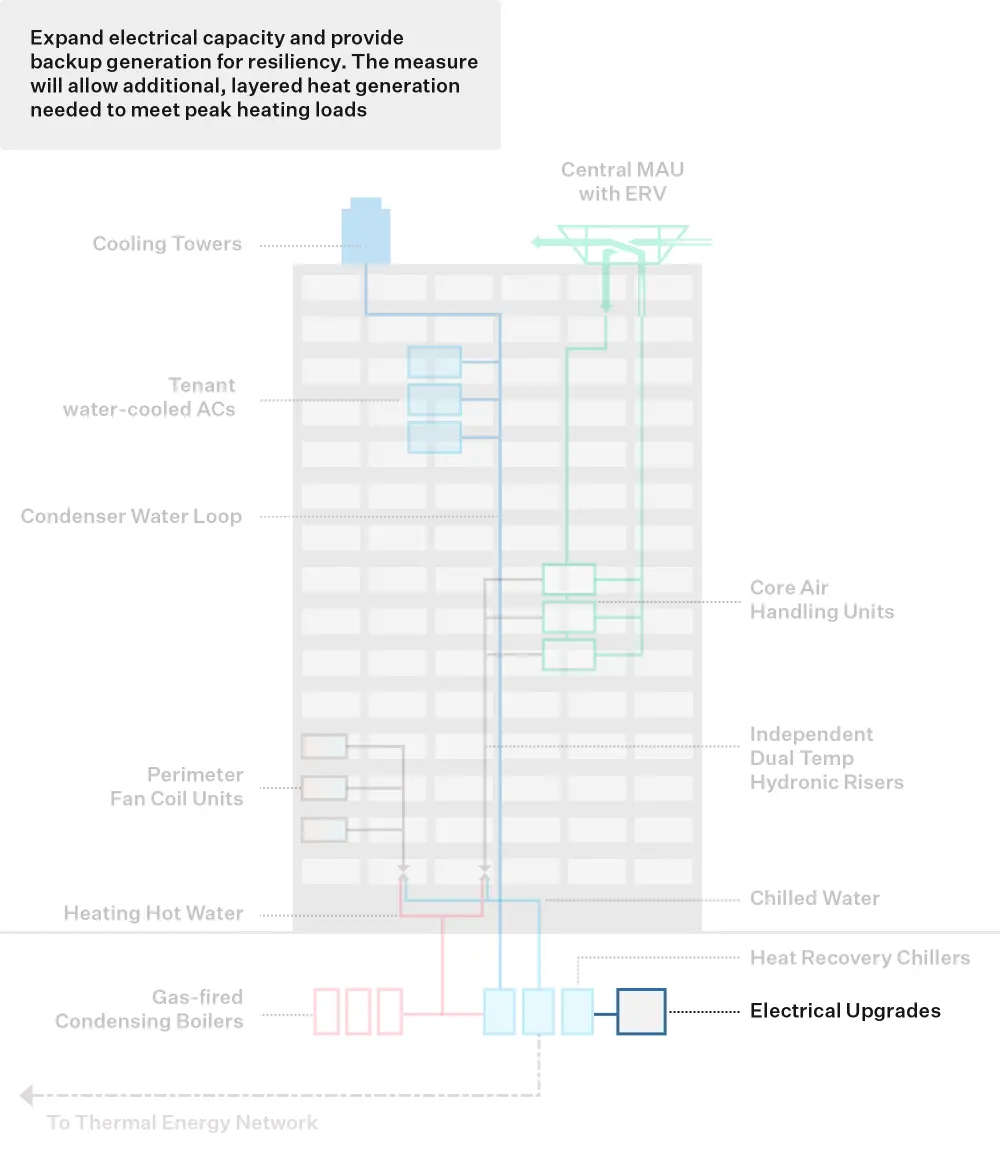

Reduce Energy Load
- Building Management System (BMS): Install new BMS for better integrated control of HVAC equipment and lower distribution temperature.
Recover Wasted Heat
The existing, inefficient 2-pipe system, which only allows the building to be in heating or cooling mode, will be re-piped to create two separate hydronic zones. This will allow the newly independent loops of the building to exchange rejected heat from the core to the perimeter zone as needed. This piping work will incorporate heat exchangers to possibly connect with adjacent buildings also owned by LeFrak that are mostly residential and create a community thermal network to share loads.
- Enabling Heat Recovery: New piping work to separate core and perimeter hydronic systems and operate them independently. Install heat exchangers to facilitate heat recovery between core and perimeter using electric modular heat pump chillers.
- Heat Recovery Ventilation: Install Energy Recovery Ventilators (ERV) to recapture wasted heat and pre-condition fresh air.
Partial Electrification
Beginning in 2024, the existing fossil fuel driven plant will be decommissioned, and a new plant that enables decarbonization will be installed, including modular electric heat pump chillers with cooling and future heating capabilities.
- Electric Heat Pump Chillers: Replace existing fuel fired steam absorption chillers with electric modular heat pump chillers that can provide heat recovery via dedicated heat exchangers.
- Thermal Network Connection: Install heat exchangers and auxiliary connection to allow a future connection to a campus wide thermal energy network.
Step 3
Step 3: Build the Business Case
Making a business case for strategic decarbonization requires thinking beyond a traditional energy audit approach or simple payback analysis. It assesses business-as-usual costs and risks against the costs and added value of phased decarbonization investments in the long-term.
Strategic Decarbonization Action Plan
An emissions decarbonization roadmap helps building owners visualize their future emissions reductions by outlining the CO2 reductions from selected energy conservation measures. This roadmap is designed with a phased approach, considering a 20- or 30-year timeline, and incorporates the evolving benefits of grid decarbonization, ensuring a comprehensive view of long-term environmental impact.
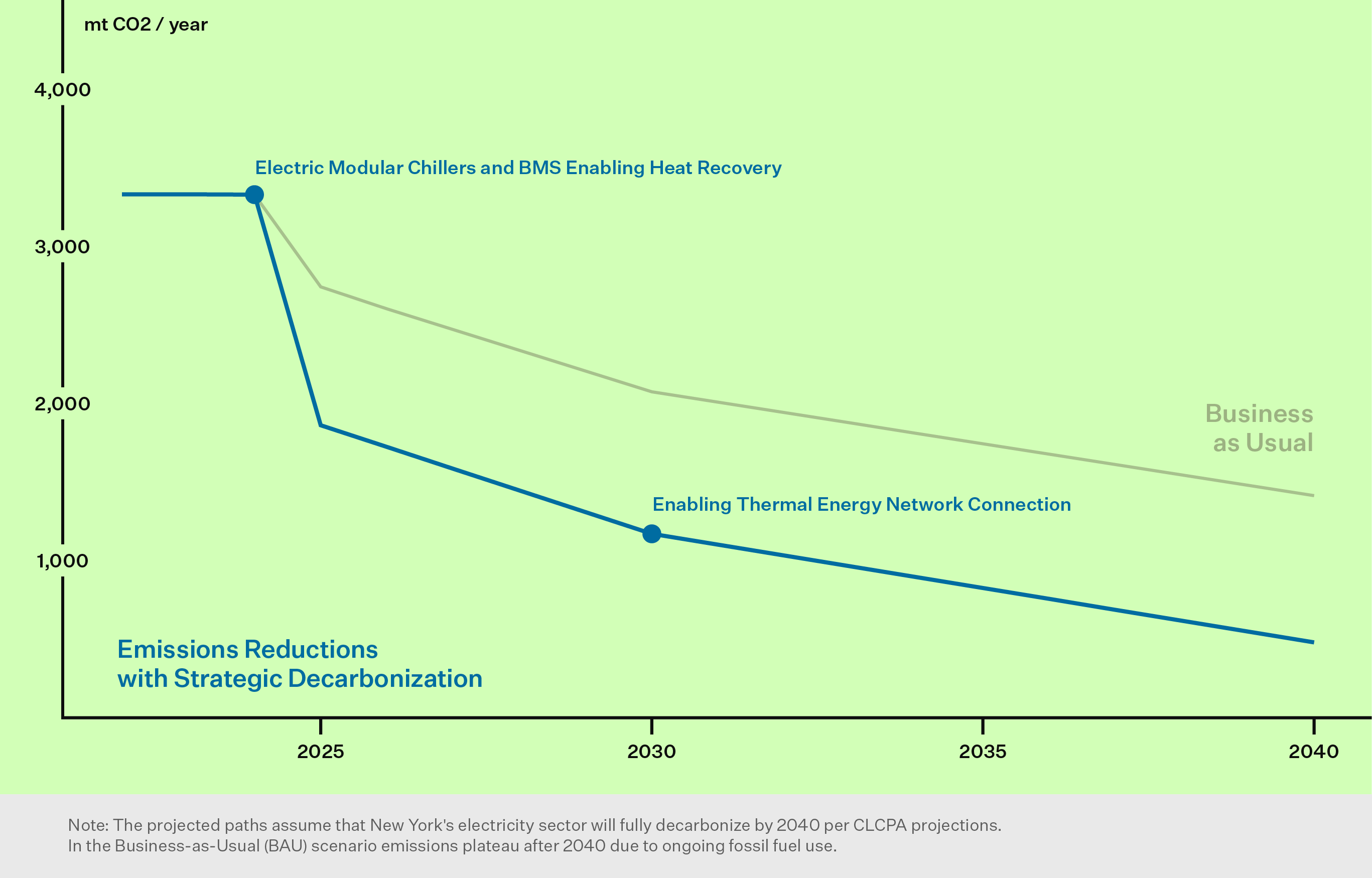
Due to external project requirements, this project had a particularly compressed implementation timeline compared to other decarbonization projects. The team evaluated various replacement options over the existing systems to reduce carbon emissions: at the end of the EBC Technical Assistance Phase, ownership reviewed the financial and technical analyses of the decarbonization roadmap options, ultimately deciding to electrify the cooling plant and enable heat recovery from the core zone to the perimeter zone. The central plant work meets the building’s immediate needs, while increasing the resilience of the central plant and allowing for future flexibility and decarbonization efforts.
On-site work to upgrade the central plants has already begun and will continue into 2025. This work includes:
- Replacing damaged steam chillers with electric modular chillers.
- Installing a new BMS system to allow better, integrated control of HVAC systems.
- Redesigned central plant with additional heat exchangers and improved piping layout to separate core and perimeter hydronic systems and operate them independently, enabling heat recovery between core and perimeter using electric modular chillers.
- Auxiliary piping and heat exchanger allowing a future connection to a campus wide thermal energy network.
- Expanded electrical capacity and backup generation for resiliency. The measure will allow additional, layered heat generation needed to meet peak heating loads.