Nordic design principles applied to New York real estate
Tags
345 Hudson, developed by Hudson Square Properties (HSP), provides a roadmap for sustainable practices by applying the Nordic design principles of holistic energy recycling and electrification. The 17-story commercial property located in Manhattan, NY was built in 1931 and features a mid-tier energy rating, aging heating system burning natural gas, and recurring carbon emissions fines starting in 2035.
The comprehensive retrofit takes advantage of tenant turnover as an opportunity to upgrade the building’s infrastructure to new, carbon-efficient, energy cost-saving technology and completely decarbonize the 856,000 gross square foot property. This project will demonstrate the power of thermal networking through an innovative approach by which heating and cooling is shared between tenants throughout the building and eventually between neighboring buildings.
Hudson Square Properties is a joint venture with Hines, Trinity Church Wall Street, and Norges Bank Investment Management, that owns 13 buildings totaling 6.3 million square feet in the Hudson Square Neighborhood.
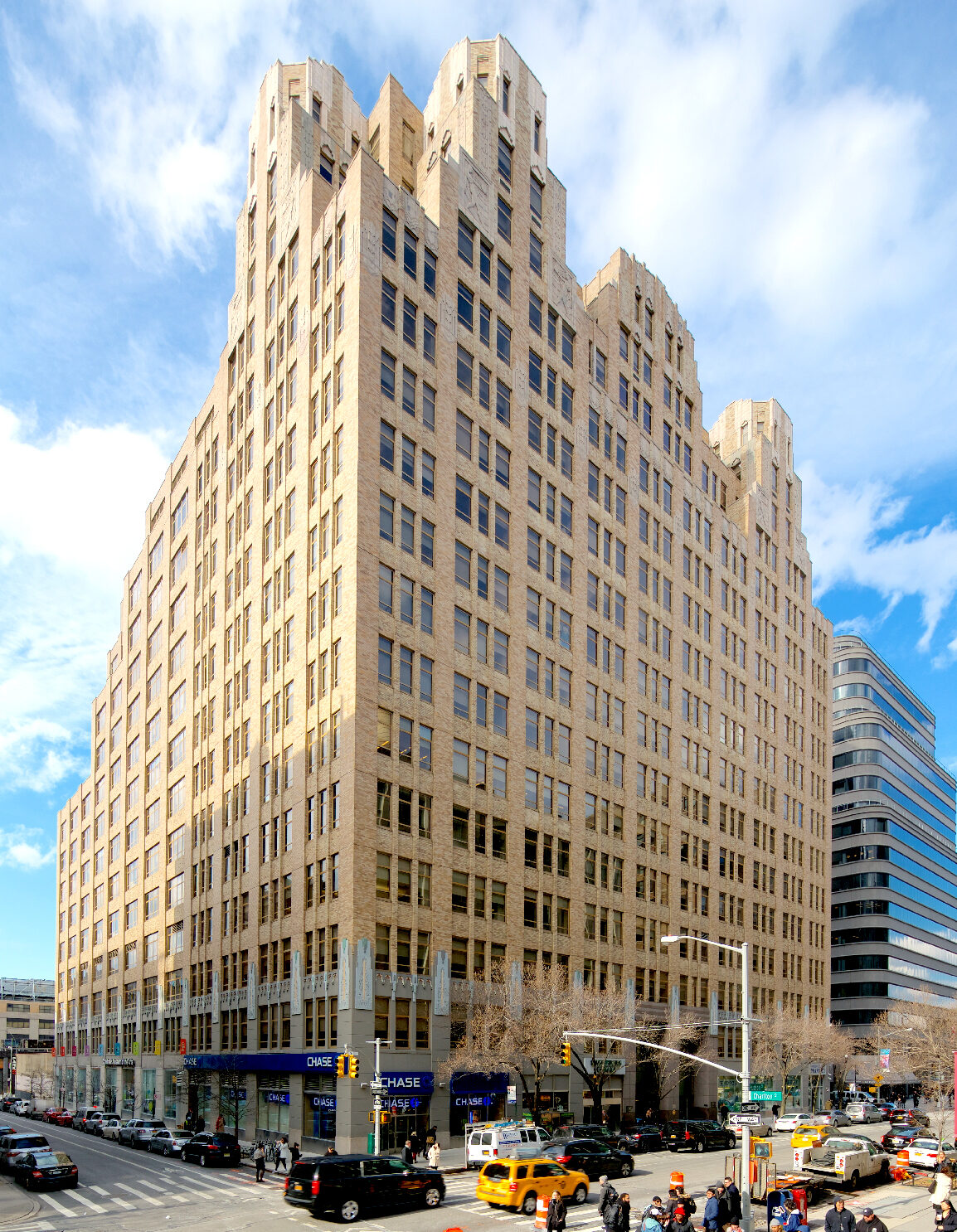
Project Highlights
Step 1
Step 1: Examine Current Conditions
A baseline assessment is key to understanding current systems and performance, then identifying conditions, requirements or events that will trigger a decarbonization effort. The assessment looks across technical systems, asset strategy and sectoral factors.
Building System Conditions
- Equipment nearing end-of-life
- Comfort improvements
- Indoor air quality improvements
- Efficiency improvements
Asset Conditions
- Repositioning
- Tenant turnover/vacancy
- Carbon emissions limits
- Investor sustainability demands
- Owner sustainability goals
Market Conditions
- Market demand changes
- Policy changes
The Hudson Square partnership is committed to future-proof its flagship property by upgrading its building infrastructure while meeting legislative climate goals and staying competitive in the commercial office market. The project team brought together a consortium of global solution providers and engineering expertise to develop a long-term retrofit plan to minimize energy usage and carbon emissions.
Step 2
Step 2: Design Resource Efficient Solutions
Effective engineering integrates measures for reducing energy load, recovering wasted heat, and moving towards partial or full electrification. This increases operational efficiencies, optimizes energy peaks, and avoids oversized heating systems, thus alleviating space constraints and minimizing the cost of retrofits to decarbonize the building over time.
Existing Conditions
This diagram illustrates the building prior to the initiation of Strategic Decarbonization planning by the owners and their teams.
Click through the measures under “Building After” to understand the components of the building’s energy transition.
Sequence of Measures
2022
2023
2024
2025
2026
2027
2029
Building System Affected
- heating
- cooling
- ventilation
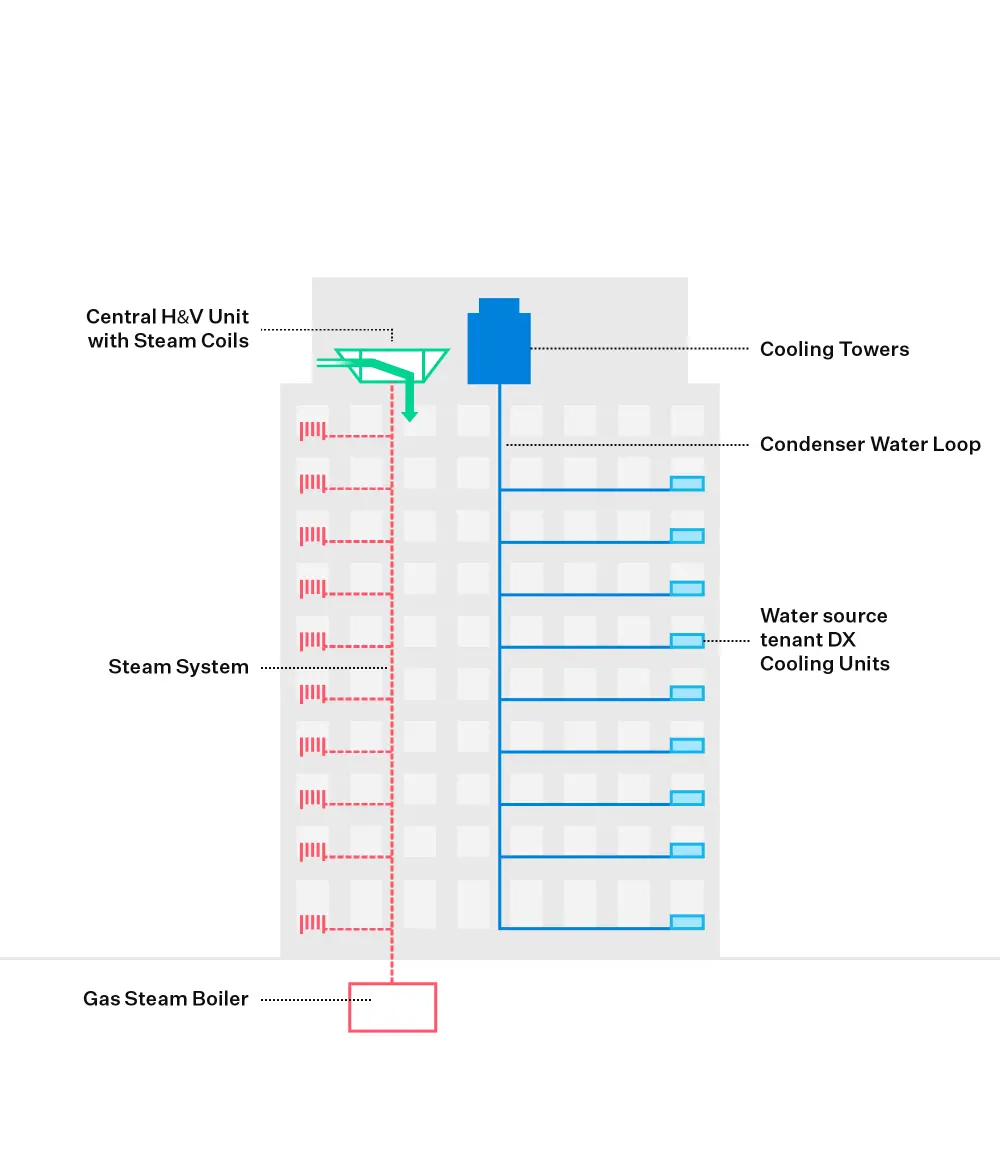
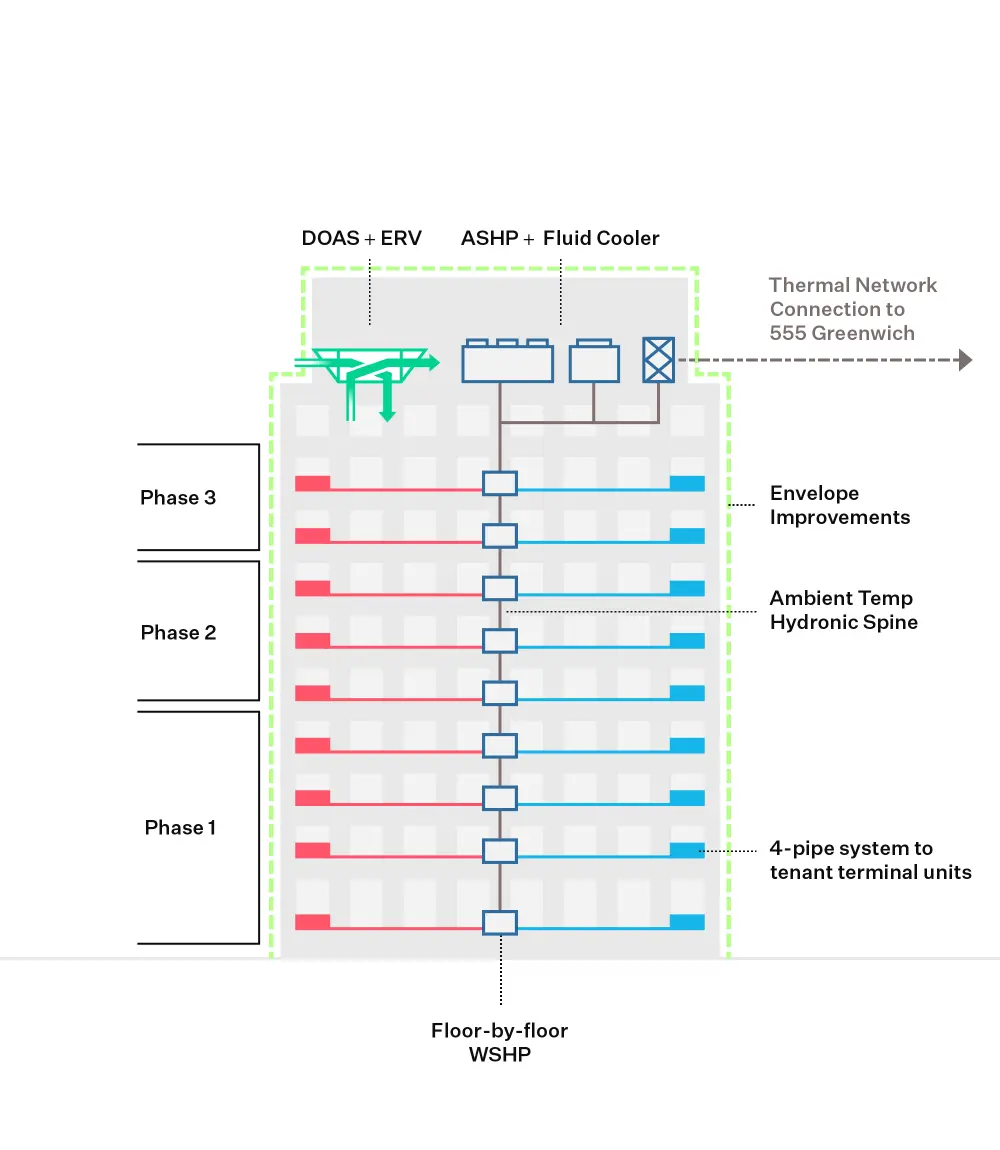
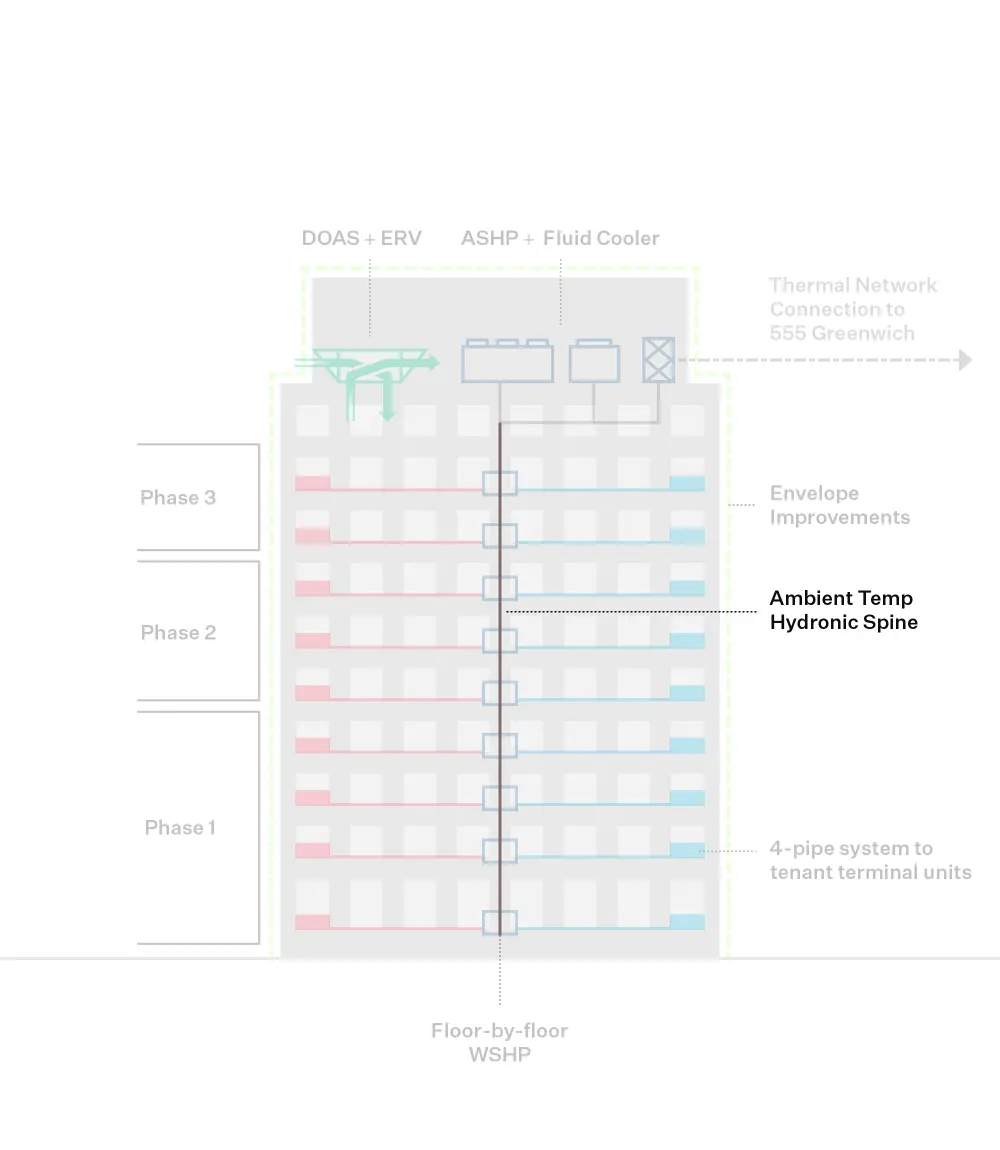
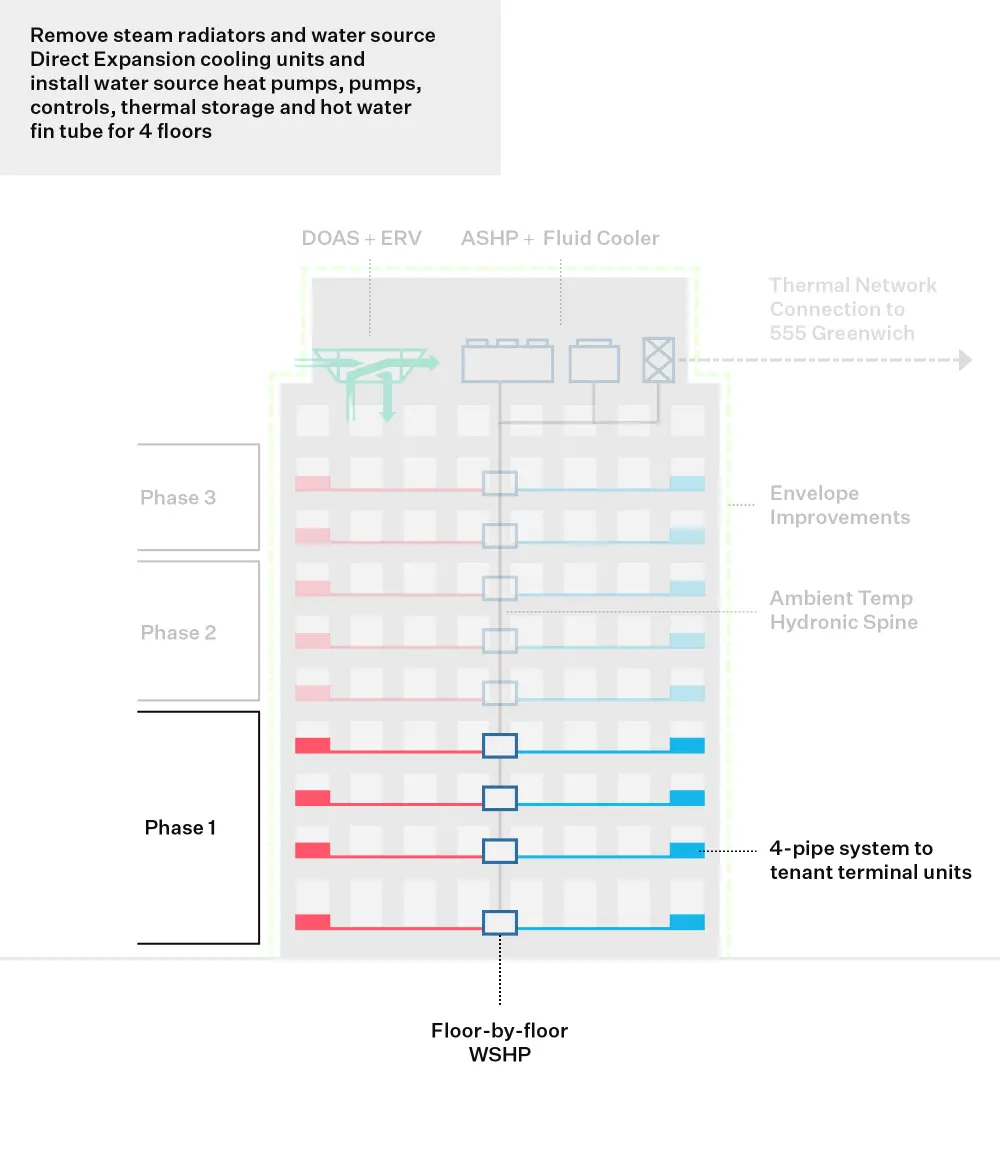
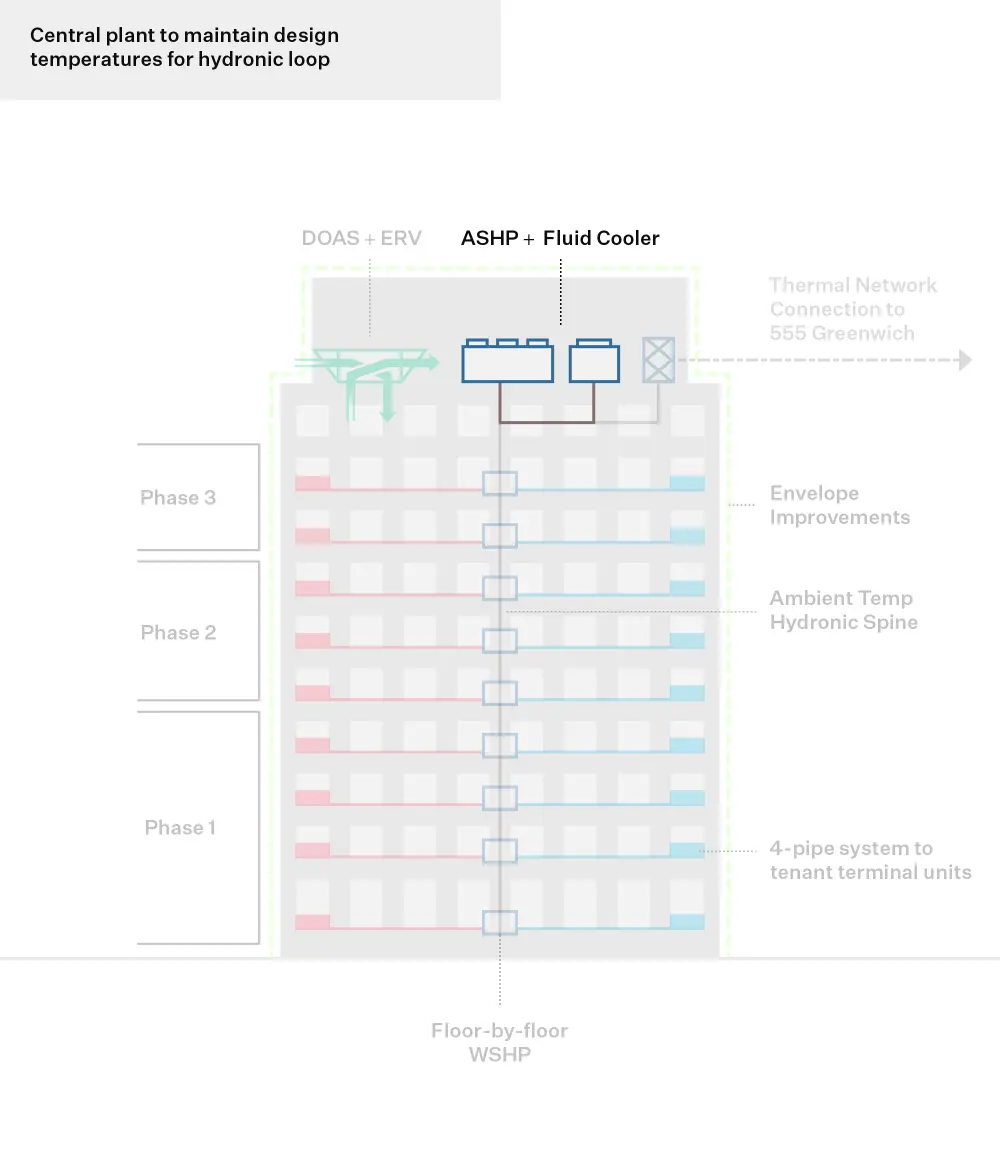
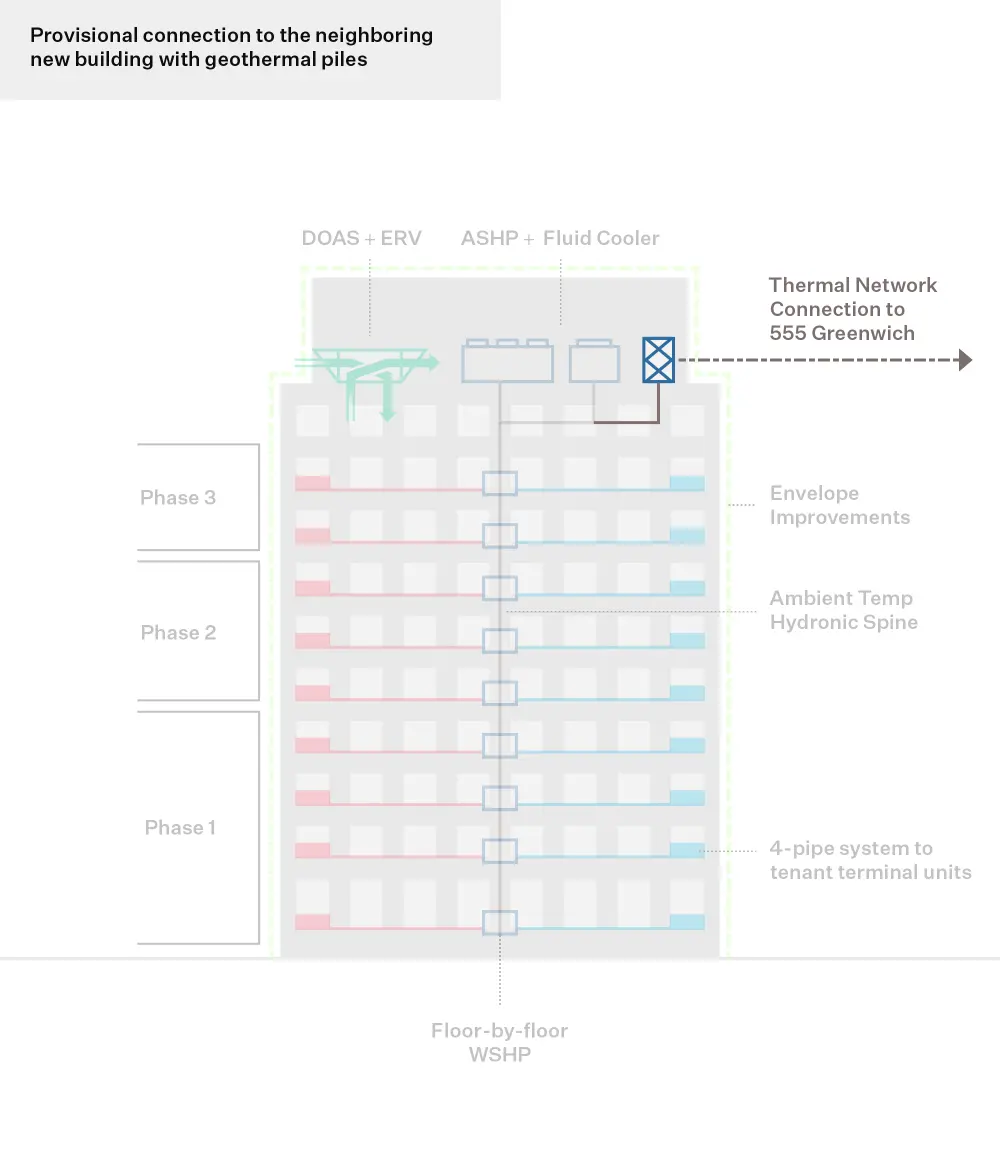
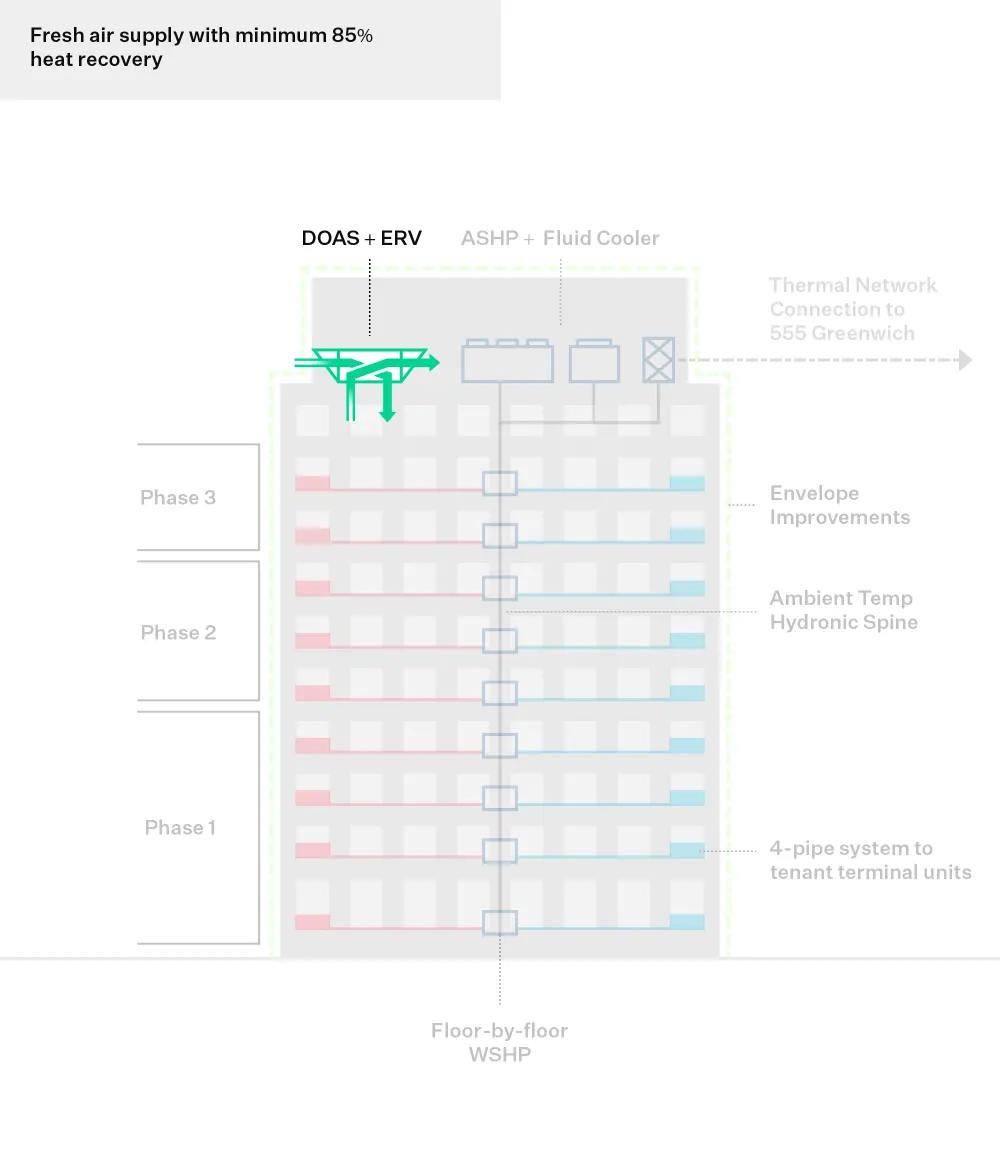
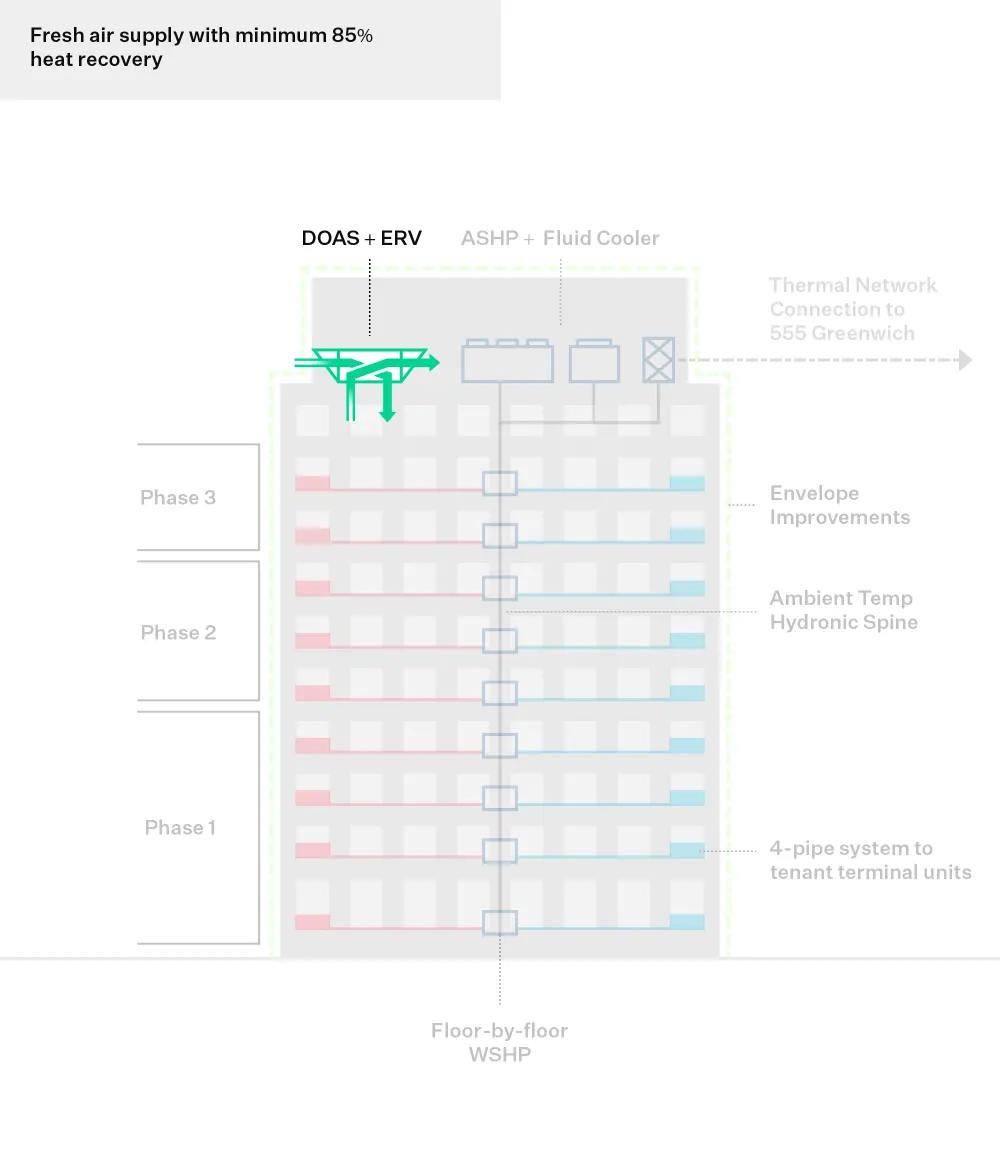
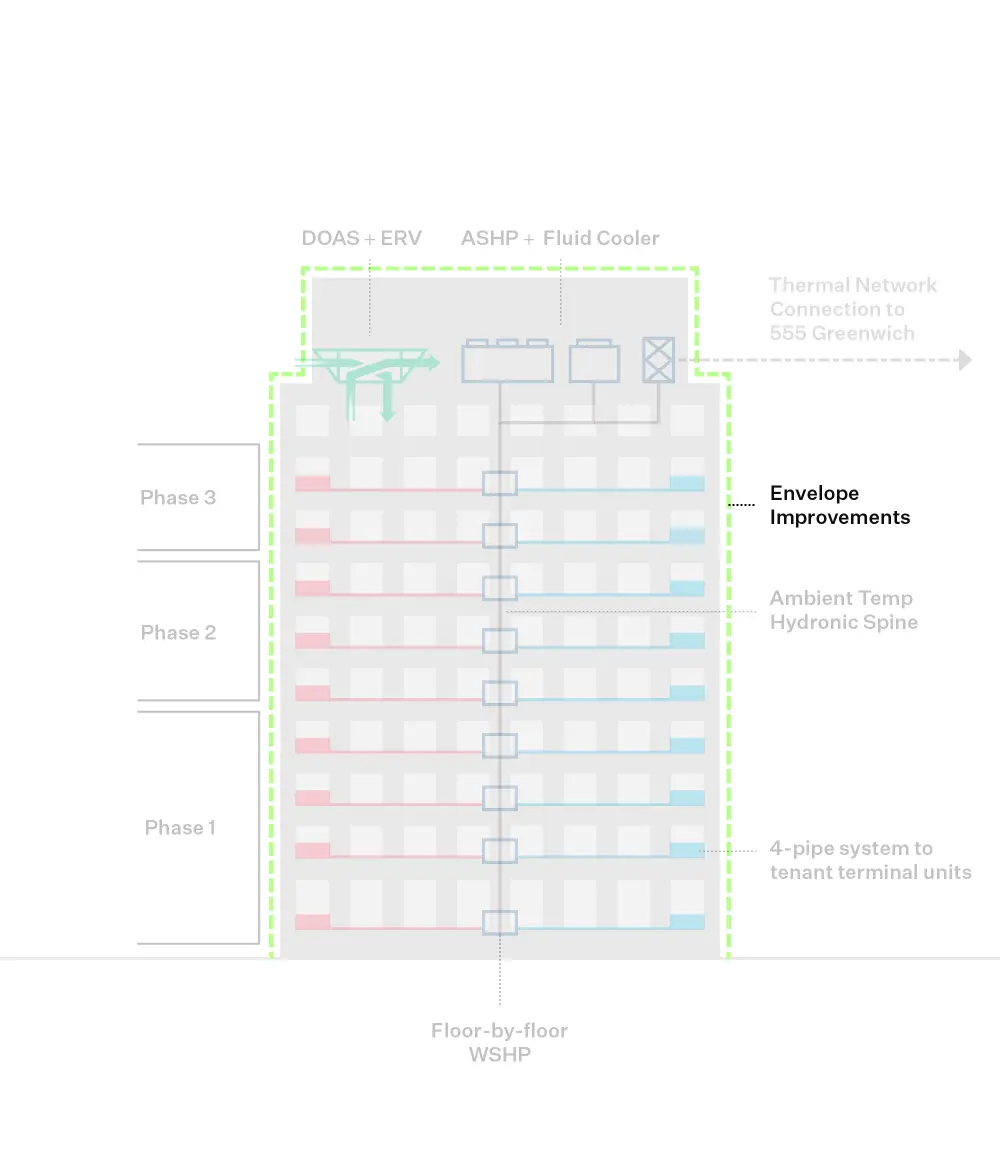
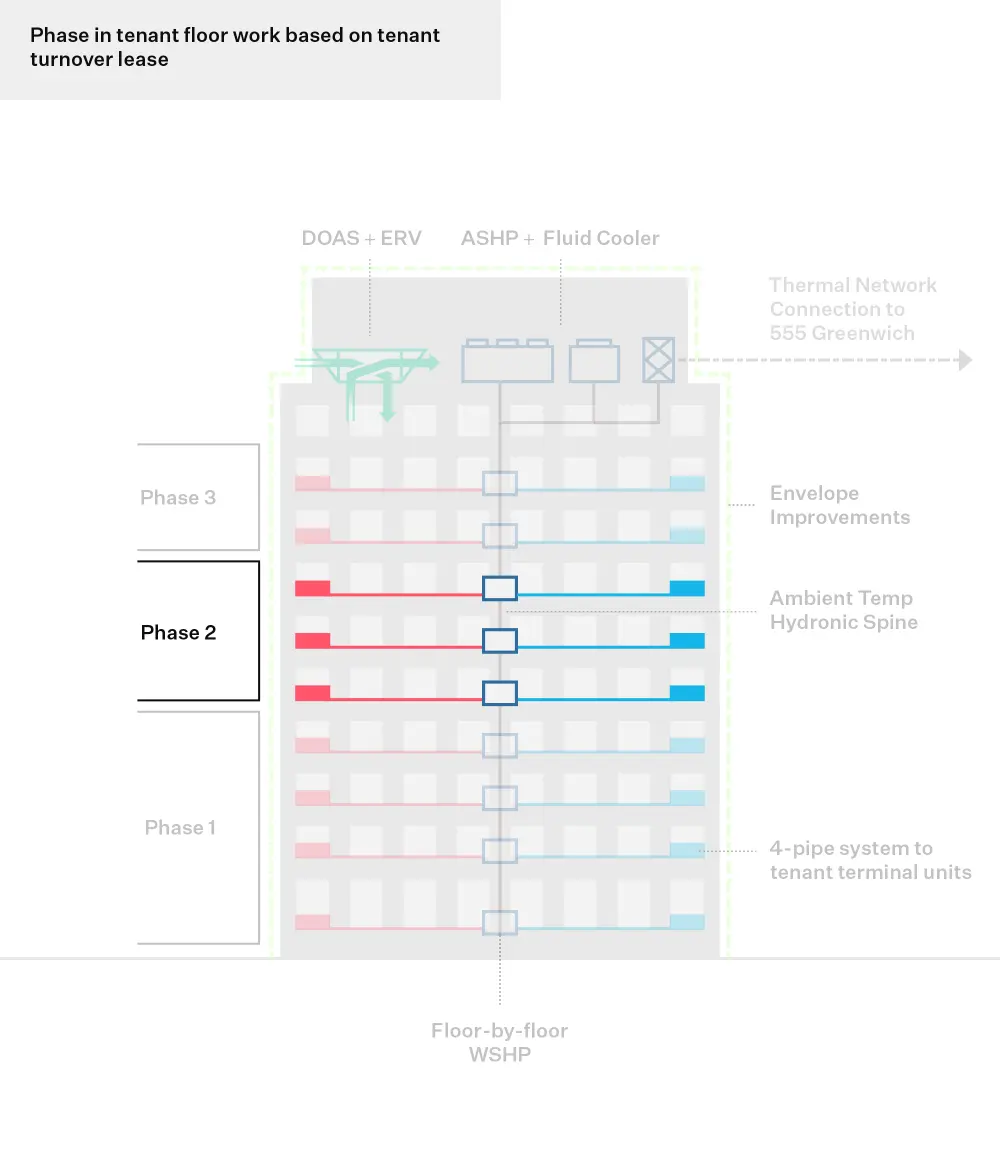
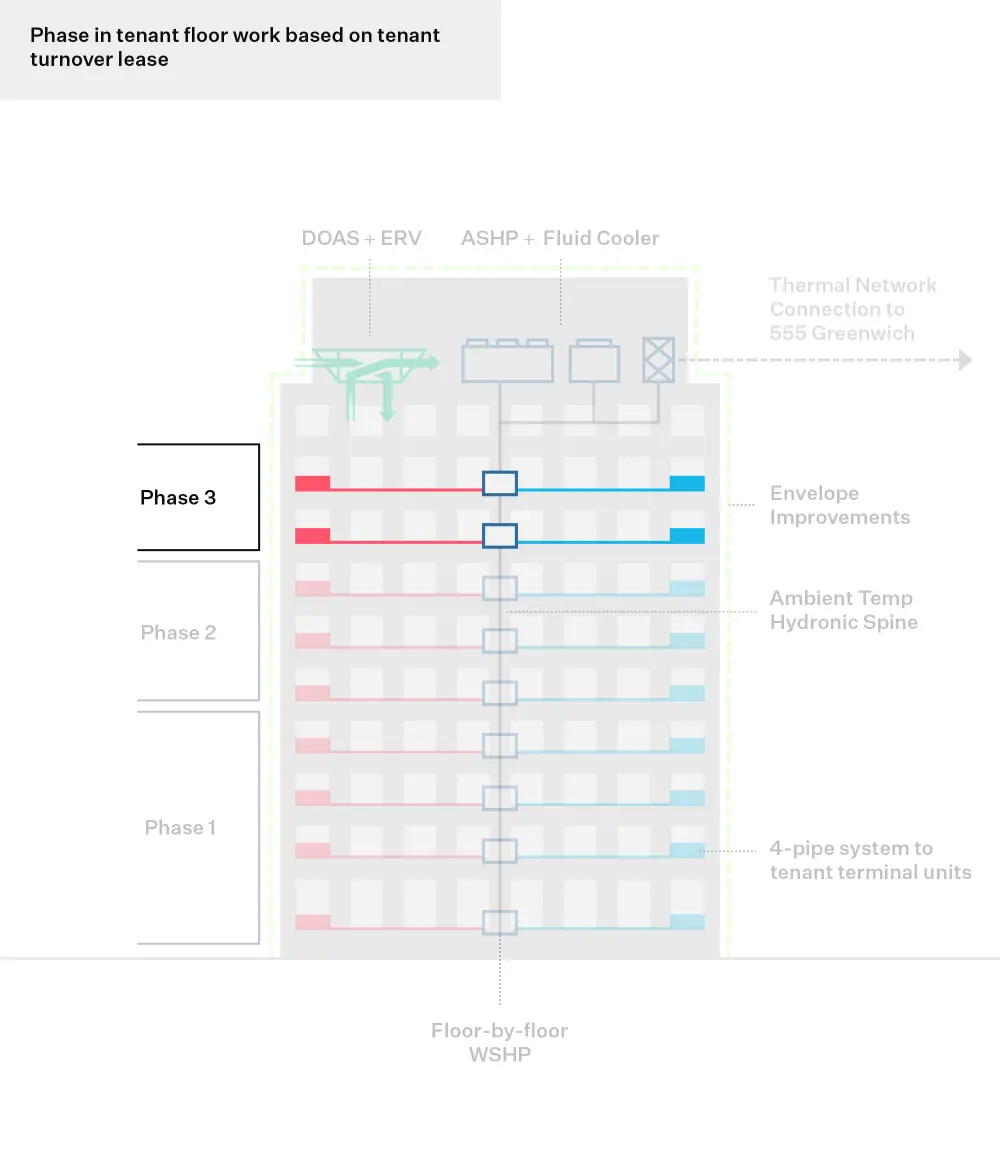
Applying the Nordic design principles of holistic energy recycling and electrification to make decarbonization technically and economically feasible over time. This design approach follows a circular systems philosophy to reduce heating demand by recovering and redistributing heat from high-energy areas to low-energy areas, rather than simultaneously cooling and heating different zones. Heat is moved to or from different floors, and only then is energy introduced to the system via air source heat pumps.
Reduce Energy Load and Recover Wasted Heat
Developing a hydronic loop operating at ambient temperatures by converting the existing condenser water riser. The ambient loop enables future optionality with the integration of different heat sources and takes advantage of simultaneous heating and cooling opportunities between spaces and floors to reuse otherwise wasted heat.
- Ambient Loop Hydronic Spine: high efficiency water-based distribution system, lower supply temperature and heat sharing between floors/zones
- Dedicated Outside Air System (DOAS) with Energy Recovery Ventilator (ERV): decouple ventilation from heat and cooling systems, and recapture exhaust air energy to condition fresh air
- Tenant Conversion: install floor by floor WSHPs and convert to hydronic low temperature heating and high temperature cooling
- Window replacement (provisional): reduce air infiltration and reduce energy loads
Partial Electrification: right-size heat pump
Leverage the high efficiency of heat pump technologies, enable grid interactivity, and take advantage of future low-carbon electricity production planned by the state.
- Central ASHP + Adiabatic Fluid Cooler: heat supply and heat rejection, maintain design temperatures for ambient loop
Full Electrification: replace/remove peak load equipment
- Thermal Storage: leverage heating hot water and chilled water storage for peak load
- Thermal network connection to neighboring building: heat sharing capability and leverage geothermal piles in the property next door
- Decommission natural gas boilers
Other Project Highlights
- Floor-by-floor replacement of packaged terminal cooling units and steam heating with a comprehensive water source heat pump system significantly reduces heating and cooling needs by recycling heat from different spaces in the building
- A more sustainable and circular approach consists of:
- Leveraging Energy Recovery Ventilation (ERV) to reduce conditioning loads
- Separating fresh air delivery and conditioning from heating and cooling systems by using a Dedicated Outdoor Air System (DOAS)
- Recycling existing sources of heat within the building during the cold weather rather than rejecting it to the atmosphere.
- Utilizing heat pumps to satisfy remaining heating loads in buildings and fully eliminate the use of fossil fuel combustion
- New systems can be phased in over time: Rather than retrofitting the entire building, work can be done on a floor-by-floor basis, which is easier on the budget, allows for greater flexibility and is less disruptive to existing tenants. It is estimated that full-floor tenants vacate spaces every 10 to 15 years.
Step 3
Step 3: Build the Business Case
Making a business case for strategic decarbonization requires thinking beyond a traditional energy audit approach or simple payback analysis. It assesses business-as-usual costs and risks against the costs and added value of phased decarbonization investments in the long-term.
Strategic Decarbonization Action Plan
An emissions decarbonization roadmap helps building owners visualize their future emissions reductions by outlining the CO2 reductions from selected energy conservation measures. This roadmap is designed with a phased approach, considering a 20- or 30-year timeline, and incorporates the evolving benefits of grid decarbonization, ensuring a comprehensive view of long-term environmental impact.
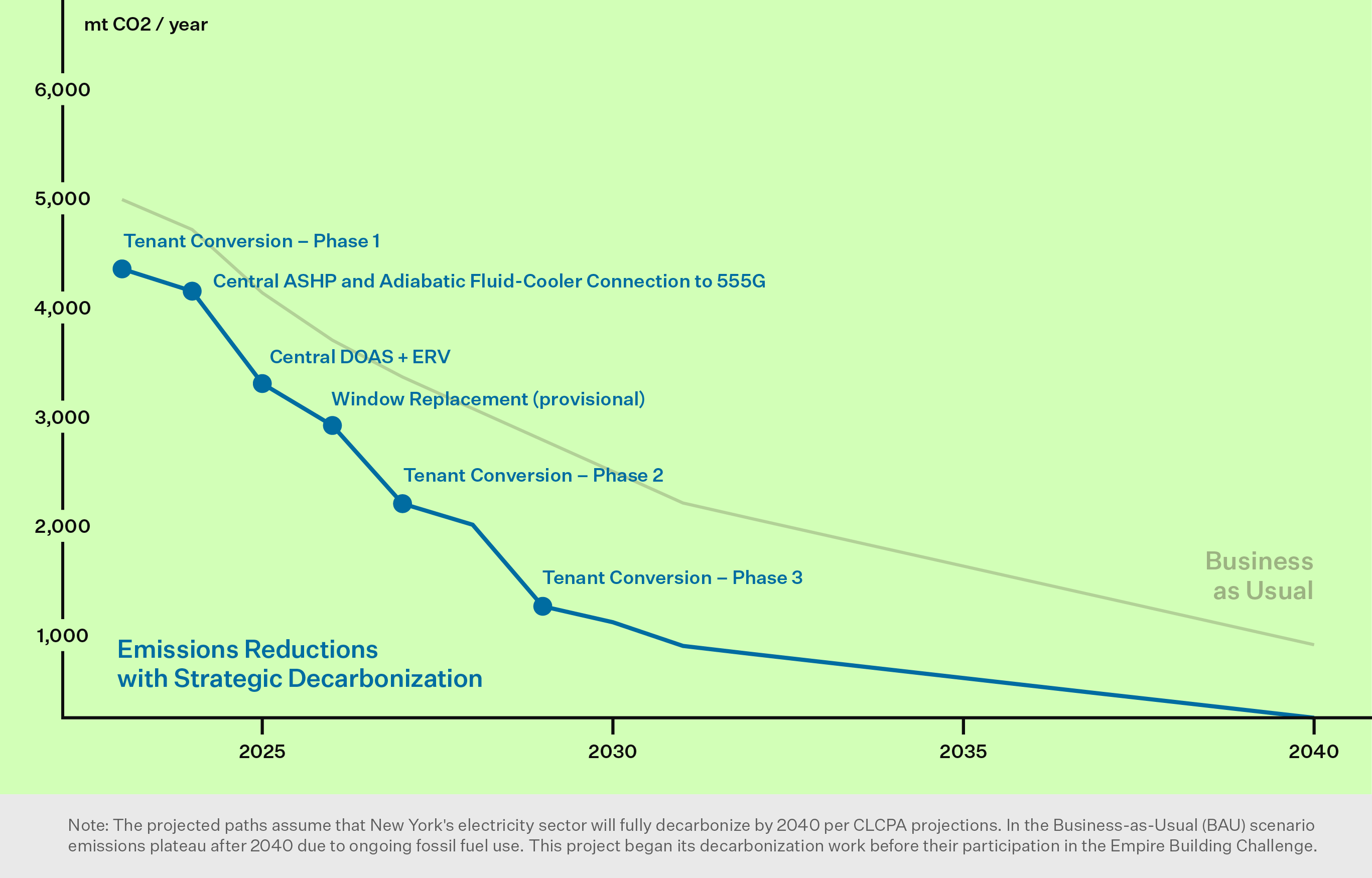
Key to HSP’s strategy was understanding how to meet aggressive climate targets while addressing the practical objectives of their tenants—stable temperatures, fresh air, and reliable equipment—without placing too much onus on tenants to devise their own solutions or diligently manage their own consumption. To devise this approach, HSP divided building systems into three distinct spheres of ownership and influence. The first sphere encompasses the heating, cooling, and air distribution equipment under tenant control (e.g., radiators, fan coil units, etc.). The second sphere includes equipment commonly installed and maintained by the landlord, but controlled by the tenant (e.g., air conditioning units). The third sphere covers the core building infrastructure, under full control of the landlord, like cooling towers, boiler plants, and primary air handling units. This framework identified a major opportunity area in which to address carbon and energy goals: equipment supplied by the landlord but controlled by the tenant. Given this, the core objective was to create a scenario in which the landlord provides the solid grounding—such as the thermal network—for tenants to condition their spaces most efficiently. With this core functionality in place, tenants are afforded efficient systems performance simply by occupying the space and tapping into the building infrastructure. Incidentally, projected long term savings will be dependent on tenant plug loads and equipment fit-outs. The potential saving values displayed above are based on best-case scenario and CLCPA carbon projections.
As floors are phased in and more tenants take advantage of the thermal network, the amount of energy recycled across the building increases, incrementally improving the efficiency of 345 Hudson. By 2035, once fully implemented, whole-building energy use would be expected to drop by more than 30%. Total building carbon emissions would fall 90%, compared to a pre-retrofit baseline, with reductions increasing towards 100% as New York’s electric grid becomes fully renewable. These reductions reflect both emissions avoided by capturing 11GWh of waste heat currently rejected by the building (e.g., via cooling towers), and via the application of high-efficiency heat pumps. With a fully deployed thermal network and energy recovery ventilation, modeling reflects a scenario in which only 4 GWh of energy would be rejected. Notably, post-retrofit peak heating and cooling loads would fall dramatically—by 92 and 63% respectively—reflecting the significant benefits of capturing, sharing, and recycling heat across floors. The thermal network is key to electrifying buildings via heat pumps, as it reduces floor-level energy demand, allowing for smaller capacity heat pump systems.
345 Hudson’s 10-year deployment plan first targets improvements to the building’s core infrastructure, then phases in tenant retrofits, floor by floor. Select vacant floors will be retrofitted up front, with the hope of providing showcases to prospective tenants and their engineering staff to witness engineering solutions applied in practice—a critical step in moving the market given the systems’ novelty in New York. From there, additional floors will be phased in during periods of tenant turnover. As the project progresses floor by floor and use of the thermal network expands, heat pumps will supplant existing packaged terminal units and efficiency will improve dramatically. Updated floors will effectively become energy producers engaging in intra- floor heat exchange, rather than receivers of linear energy supply, benefiting the overall system. By 2025, HSP aims to connect the ambient loop at 345 Hudson to the neighboring building at 555 Greenwich, to share loads as needed and take advantage of its geothermal system. By 2030, the building will operate using only electricity, and take full advantage of the fully formed thermal network across all floors. With all floors connected, the thermal inertia (the energy stored within the hydronic network itself) of the whole building will often be substantial enough to store or release energy in response to changing utility rates or renewable energy generation—importing or exporting heat energy when needed, particularly during peak demand conditions. Reactive to grid demands, this solution allows the building to become an asset to the grid rather than simply a consumer.