This report, produced by Urban Land Institute’s C Change program, illustrates how lack of alignment on decarbonization approaches between property owners and occupiers is hindering progress to decarbonize and has the potential to increase emissions in the medium- to long-term. These findings underscore the need for stronger partnerships and closer collaboration between occupiers and owners.
Building Typology: Office
Urban Green Council’s Grid Ready: Powering NYC’s All Electric Buildings 2021 report sheds light on how power is delivered to NYC, examines how heat pumps will change electricity demand in buildings, and shows how electrification can be rolled out to carefully manage increasing demand. Additionally, their interactive Grid Ready Mapping Tool allows users to visualize how power demand will grow as fossil fuel heating systems are replaced with electric heat pumps.
Tags
If a Letter of Intent (LOI) is used, commercial real estate brokers can incorporate a simple and concise clause, such as the sample provided, to ensure that both the building owner and tenant are committed to working together to implement carbon emissions reduction strategies.
This resource is part of a series of actionable resources developed for the Decarbonizing New York City Offices project, an initiative dedicated to reducing carbon emissions in leased commercial spaces by facilitating meaningful collaboration between building owners, tenants, brokers, lawyers, designers and others involved in leasing and office utilization decisions. Learn more about the initiative: www.be-exchange.org/decarbonizing-new-york-city-offices
Tags
The goal of the kickoff phase is to set the team up for a successful decarbonization project. In this early stage, project teams should come to consensus on the following:
- Energy and emissions reduction targets
- Desired economic outcomes
- The project workplan, schedule, and key milestones
- Required skills and capacities
- Gaps in expertise and who will be brought onboard to fill them
A critical outcome of this phase is building trust through shared goals and open, honest dialog about the building’s current state and what the building owner hopes to achieve through the project. In addition to building consensus and understanding with external consultants and service providers, aligning goals across the building owner’s various internal divisions is a necessity. Senior management must set a tone that celebrates opportunities for continued improvement across finance, asset management, operations, and on-site staff.
At the end of this phase, the team should have a clear understanding of goals, a well-defined work plan with key milestones, clear roles, and the beginnings of a trust-based relationship that will support creative problem solving.
Build the Team, Set Goals and Timeline
Inputs
To set the project up for success, a point-person from the building should be identified. This person will be responsible for setting expectations with the consultant team, communicating with leadership within the real estate organization, and working with the building operations team to support data collection activities.
Activities
During the kickoff phase, activities include:
- Identifying the team, including internal resources and external service providers.
- Getting educated on the latest energy and carbon trends and requirements.
- Conducting a formal kickoff meeting to set goals, define processes, and establish a project timeline.
- Establishing a tenant engagement strategy.
Outputs
Deliverables from this phase can take many forms, including kickoff meeting presentation slides and notes, a formal workplan, a Gantt chart, or some other means of communicating the key project objectives and milestones. The team is now ready to dive into the deep energy retrofit.
Lessons Learned & Key Considerations
- Establish clear objectives: Outlining a clear set of objectives based on technical and economic needs specific to each building early in the process creates clarity on project workload, the types of expertise that will be needed, and the time required to complete the work.
- Select a team that will collaborate across disciplines: Building decarbonization is a multifaced and challenging effort. The team should comprise members who are eager to work and collaborate across disciplines.
- Include the building operations staff: Understanding the nuances of how the building operates is an important part of the investigation and energy modeling phases of the project. Include the building Chief Engineer and key operating personnel in the kickoff meeting and other key milestones.
- Engage tenants: Beyond the immediate team, it is important to consider how and when to engage the building tenants. Even with the most efficient equipment, a building will not achieve deep energy and carbon reductions without tenant buy-in and action.
- Connect with contractors, equipment manufacturers and subject-matter experts: Secondary support from these groups can often be very helpful because they bring additional expertise and a different perspective from those in the core project team.
Tags
The Inflation Reduction Act includes some two dozen tax provisions that will save families money on their energy bills and accelerate the deployment of clean energy, clean vehicles, clean buildings, and clean manufacturing. The table linked here (last updated September 21, 2023) provides the key information about these tax provisions and links to the latest announcements related to their implementation.
Tags
Commercial properties have long struggled with simultaneous heating and cooling needs across a single building, and even across a single floor. New models for sharing heat across building occupancies offer significant performance improvements. Some of the most successful models have been utilized in the Nordic countries for many years and are directly aligned with the Resource Efficient Decarbonization (RED) framework developed by NYSERDA, which encourages a holistic approach to decarbonization that is founded on reducing demand and sharing heat across tenants, buildings, and districts. Advancing this approach across the US market could be a critical component of meeting our climate action goals.
During this High Rise / Low Carbon series program developed to support the Empire Building Challenge and other NYSERDA programs, industry experts will feature innovative strategies for heat recovery and discuss the importance of these strategies in reducing energy waste, peak load demand, and energy cost, in line with achieving high performance retrofits of large buildings.
Opening Remarks
Susanne DesRoches, Vice President, Clean and Resilient Buildings, NYSERDA
Moderator
Molly Dee Ramasamy, Head of Deep Carbon Reduction, Jaros, Baum & Bolles
Presenters
Mike Izzo, Vice President, Carbon Strategy, Hines
Elizabeth Moronta, Senior Vice President of Development, Omni New York LLC
Adam Friedberg, Principal, Buro Happold
Miguel Gaspar, Vice President/Group Leader, Loring Consulting Engineers
Samuel Long, Innovation Specialist, Danfoss
Tags
Insights from Empire Building Challenge
This guide describes the three-step financial analysis process that a building owner can follow to determine the best path forward to decarbonize their property. The objective of the financial analysis is to evaluate the cost-effectiveness of distinct decarbonization pathways and implementation timelines. This means finding the most cost-effective or lowest cost pathway(s) to decarbonization, as opposed to evaluating packages of energy conservation measures (ECMs) for simple payback, or solely identifying cost-effective energy efficiency improvements. The overall cost-effectiveness of the decarbonization plan will be determined by the technical approach, the alignment with the broader capital plan and asset management approach, as well as the phasing and implementation of interventions.
This workstream brings together the technical and economic data on energy and carbon reduction measures to create a holistic techno-economic evaluation of the CO2 reduction opportunity that meets a building owner’s return on investment criteria. It incorporates all costs and savings associated with individual ECMs, and the bundling together of ECMs into “ECM packages”, as well as the development of a phasing or implementation plan to align with asset management opportunities.
Read more about the three-step process below:
1. Build the Financial Base Case and Calculate Business-As-Usual NPV
A financial model is a decision-making tool to help the project team identify which ECMs should be packaged together to optimize carbon savings and mitigate higher cost of some synergistic ECMs. A discounted cash flow calculation can be used to aggregate the incremental cash flows associated with each proposed ECM and calculate the net present value (NPV). These incremental cash flows include all positive and negative cash flows associated with the ECMs (e.g., capital costs, utility cost savings, repair and maintenance savings, incentives, and avoided LL97 fines in the NYC context, etc.) and are distributed over time according to when the cash flow will occur. The NPV of each package of ECMs can then be calculated as the sum of the NPVs of each individual ECM included in the package. NPV, along with other important metrics like cumulative carbon emissions reductions, will be used to determine the optimal retrofit solution.
Inputs
- Baseline Energy Consumption and Utility Costs: The adjusted baseline energy model and associated energy consumption should be utilized to determine the baseline utility costs. This information can be obtained directly from the energy model and is the reference point from which all energy savings for the proposed ECMs will be calculated.
- Building Operational Expenses Budget: Defining what this budget would be under the business-as-usual scenario is necessary to understand the impact of a potential ECM on current operational expenses. This budget should cover expenses for any regular maintenance of the existing building systems and be forecast through the duration of the financial analysis study period.
- Building Capital Expenses Budget: Given the lifespan of current building equipment and components, there should be an existing budget for the replacement of equipment reaching end of life. Reviewing this budget is beneficial to the project team as it will highlight opportunities to synchronize the implementation of ECMs with the existing budget and provide access to an additional pool of funding that may otherwise not be available.
- Discount Rate: The building owner should provide the discount rate to be use in the financial model. This rate will be used to determine the net present value (NPV) of future cash flows associated with the implementation of ECMs. Because NPV calculations are highly sensitive to the assumed investment rate of return on capital, this variable should not be assumed.
- Utility Escalation Rate: Utility escalation rates should be applied to the baseline utility costs of the building to capture projected increases in utility rates throughout the study period. Typical electrical escalation rates can range from 3% to 5%, while fuel escalations can range from 1% to 2%. It may be beneficial to review historic annual energy bills to fine tune these escalators for your project.
- Construction Escalation Rate: This rate typically ranges between 2.5% – 3.0%, but may vary depending on the duration of the study period and the specific technologies and industries involved in the implementation. For example, a zoning change that fuels a construction boom could increase this factor as could a recovery from a recession.
- Time Horizon for Financial Model: The project team and owner must establish a time horizon for the financial analysis. This will be informed by the expected payback period for ECMs, the implementation timeline anticipated for certain ECMs (i.e., those that would most economically be completed at the time of tenant lease renewal), as well as project objectives associated with meeting LL97 emissions limits or other similar goals. A ten year time frame is a reasonable starting point, however a longer view often creates substantially more carbon reduction.
Activities
- Incorporate Known Inputs into the Financial Model: Prior to the inclusion of ECMs into the financial model, the financial base case can be constructed for “business as usual” operations. Given the building’s current energy consumption and associated energy cost, the operations and maintenance budget, the capital expenses budget, and the anticipated fines associated with LL97, it is possible to get a sense for what the building will spend during the study period using and maintaining the existing systems. This will be the baseline against which all ECMs and their associated incremental cash flows are compared. The business-as-usual financial model should be reviewed with the building’s financial and operations teams to ensure that all inputs have been accurately interpreted and incorporated.
Outputs
- Net Present Value (NPV) of the Business-as-Usual Case: Using all known information about the building (utility costs, repairs and maintenance budget, capital expenditures budget, anticipated LL97 fines) it is possible to calculate the NPV of business-as-usual operations. It is important for the project team to highlight to the client the cost of “doing nothing” or not implementing any ECMs as it relates to LL97 fines. This will be the financial baseline against which all proposed ECMs and ECM packages will be compared.
Key Considerations
- Select and Verify Financial Model Inputs: The owner should be involved in the setup of the financial baseline model to ensure the correct inputs are used. The owner will need to provide the project team with the discount rate to be used for the analysis, the current maintenance and capital expenditures budget, and can provide input on the recommended study period and construction escalation rate.
- The Business-As-Usual case should also consider the cost of inaction: There is a cost to inaction. Cities are increasingly following New York City and limiting or increasing the cost of carbon emissions from large buildings. Over time, equipment will age and require replacement, while tenant expectations will evolve. Buildings that do not plan for decarbonization are taking on risk they have not quantified.
- Time horizon for financial model should be as long as possible: The longer the time horizon, the more optimal carbon reduction strategies will emerge. A minimum of 10 years is recommended for this type of analysis.
2. Obtain Pricing and Conduct Preliminary Economic Analysis of ECMs
Once pricing and energy cost savings are obtained for every ECM, a preliminary calculation of the net present value (NPV) can be performed. This will give the project team immediate insight into the economic viability of the proposed measures, although these values should be used only as indicators at this point. The final NPV calculation should also include maintenance implications, rebates, and LL97 fine avoidance. Nonetheless, these preliminary NPV values along with the carbon reduction impact of each measure can be used to assess and refine the final list of recommended ECMs.
The steps in this section can be summarized as:
- Develop preliminary estimates of capital, operational, and maintenance costs associated with each ECM identified in the technical analysis.
- Use the same discount rate for the base case analysis to calculate the NPV of each ECM and yield an initial sense of its energy and carbon reduction potential that meets business needs.
Inputs
The financial baseline model is the point of reference for all subsequent analysis of proposed ECMs. Any energy cost savings associated with an ECM will be deducted from the baseline energy cost.
Preliminary ECM Energy Savings and Energy Cost Savings: Once each individual ECM has been run in the energy model, energy consumption and savings information will be available. Utility cost outputs can be used to calculate the associated energy cost savings of each measure. The energy consumption savings of each measure will be deducted from the baseline to calculate the overall reduced energy consumption of the proposed model for every year of the study period. The energy cost savings will be used as a critical input in the calculation of the NPV for each measure.
Activities
- Distribute Energy Cost Savings for All ECMs: Energy savings and associated energy cost savings should be distributed across the implementation timeline for each ECM. For example, if a measure is intended to be implemented over the course of tenant lease roll, then the anticipated savings would be distributed across those years as opposed to realized all at once. Utility cost escalators should be applied to ensure that the savings associated with increasing utility rates are captured appropriately. Accurate distribution of the energy cost savings across the study timeline will impact the NPV calculation for each ECM.
- Determine Capital Costs for All ECMs: – The capital costs of all ECMs will need to be captured in the financial model as it is a critical input into the net present value (NPV) calculation. Pricing quotes can be obtained directly from an equipment vendor, but should also capture costs associated with controls and integration into the BMS, as well as associated installation costs. For example, while a vendor may be able to easily calculate the cost for replacing insulation on a piping riser, the true of cost of the measure may need to include the cost of removing and replacing the shaft wall and any potential asbestos abatement work. If the existing insulation is in poor condition and needs repair soon, the ECM cost might simply be the cost differential between restoring the original insulation value and improving it as well as the NPV impacts of an accelerated timeframe of the overall expenditure. For this reason, general contractors or cost consultants should be involved in determining the full cost of an ECM.
Pricing information can also help inform the details and development of the ECMs. The equipment vendors or cost consultants may have suggestions on how to reduce cost of ECMs while preserving the design intent and performance of the measure. Cost consultants should also provide input on which ECMs should be implemented together to reduce costs associated with general conditions.
- Calculate Preliminary NPVs for All ECMs: Pricing information and utility costs savings from the energy model can be used to quickly calculate a preliminary NPV value for each ECM. This will provide deeper insight into the financial performance of the ECM and allow for comparison between ECMs.
While this information is helpful for the further development of ECMs and the sequencing and packaging exercise, the project team should remember that these are not the final values. The complete NPV calculation should include maintenance cost implications, potential rebates and incentives, and anticipated LL97 fine avoidance which may change the financial picture of individual measures.
Necessary capital work that does not have an energy efficiency or carbon emissions benefit and can be superseded by a proposed ECM should be included in the BAU cashflow analysis to avoid underrating the potential performance of proposed ECMs. This is another reason it is critical to know of all planned or required major capital expenditures in the BAU case.
Outputs
- Analysis of Capital Costs and Energy Cost Savings for All ECMs: The analysis of initial capital costs and energy cost savings for all ECMs under evaluation can provide the project team with useful feedback about which measures provide standout savings and conversely, costs.
- For ECMs with high capital costs, review the pricing estimate in detail and ensure that costs are not being accounted for twice. Reach out to the cost consultant and see if there is any way to alter the implementation of the ECMs to consolidate and reduce first costs.
- For ECMs with high energy cost savings, review the savings with the energy modeler to ensure that assumptions are as accurate as possible and not inadvertently inflating the cost savings results. Energy cost savings results should be reviewed in tandem with carbon emissions reduction values to understand how these values are correlated.
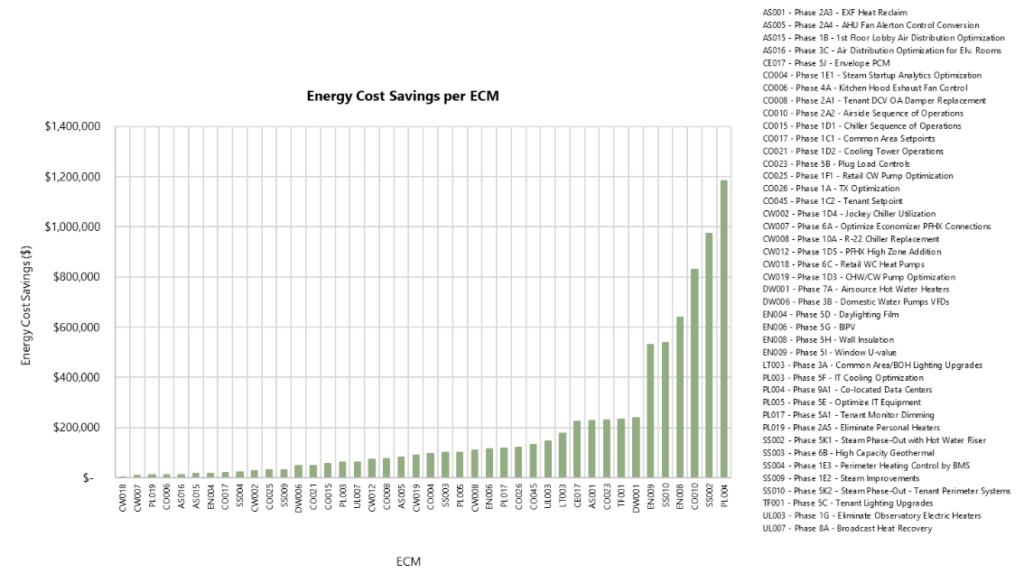
Figure 1: Energy cost savings of each ECM. Source: Empire State Realty Trust
- NPV for All ECMs: Individual NPV results for all ECMs are beneficial for the quick assessment and comparison between ECMs. The magnitude of the NPV and its sign (positive vs. negative) helps the project team understand the size of the prize and the ease of capture. These values will be used to inform the packaging process described in the Group, Sequence, and Package ECMs section.
Figure 2: The net present value of all ECMs. Source: Empire State Realty Trust
Lessons Learned & Key Considerations
- Determining the cost effectiveness of a decarbonization plan requires more than simple payback calculations: Cost effectiveness is about more than simple payback calculations. It is about finding the most cost-effective pathway to decarbonization, not just “combining ECMs to find payback”. Finding the most cost-effective pathway to decarbonization entails identifying the ECMs necessary to decarbonize and then the development of a realistic plan that accounts for real estate disruptions, existing equipment end of useful life, and CapEx/OpEx financing realities to identify an ECM phasing schedule that balances change and asset continuity.
In Practice
Empire State Building Case Study3. Refine Projections and Make Recommendations
The complete techno-economic analysis of the ECMs is developed by including the final energy modeling results – in the form of energy, utility, and carbon savings – and revised estimates of costs to update and expand the financial model. This includes revised energy costs, maintenance costs, LL97 fines, refined capital and implementation costs, incentives, and any other costs/savings the team believes will be incurred. The team will need to use judgement, experienced advisors and those familiar with local labor, permitting and logistics costs. These parameters will be used to calculate the NPV of each ECM proposed, and as well as for each package under consideration. Once all costs and benefits have been identified the team can create final versions of the analysis charts for the ECM and ECM packages that allow the team to evaluate the tradeoffs between greater CO2e reduction and NPV impact, LL97 fines and the impact of grid decarbonization. Along with the carbon reduction potential of the packages, these results will be evaluated against the project objectives. At the end of this exercise the project team should determine which package they will recommend to the client based on an optimization of cost, carbon reduction, and achieving the pre-established project objectives.
The steps in this section to get to the final recommendations can be summarized as:
- Segment the ECMs by using a simple matrix that differentiates between the magnitude of the carbon reduction and the NPV impact. Doing so will help focus the team on the largest impact measures and stimulate problem solving for those measures that could have a large potential impact but are not currently NPV positive. For example, prioritizing measures that reduce load on HVAC systems, so that smaller HVAC systems can be utilized, improving the NPV.
- Create ECM packages that are logically grouped by implementation sequence, subsystem co-dependencies (e.g. air-side improvements), cost savings (e.g. open a wall once) and the potential to increase CO2e reduction while still meeting financial targets (e.g. NPV >= 0).
- Calculate the NPV of these packages and compare to the base case financial model and the carbon reductions.
Inputs
- Updated Energy Savings and Energy Cost Savings: Energy savings and energy cost savings for each measure and each package under consideration should be updated and added to the financial model. These are direct outputs from the final modeling results from Workstream 2 “High Resolution Energy Modeling and CO2 Analysis”.
Note that the same ECM may have different energy savings associated with it in different packages depending on which ECMs are included within the package. The energy cost savings should be applied across the study period according to the implementation timeline and the project team should consider delaying the savings by six months to one year, taking care not to “claim” savings too early. Appropriate utility cost escalators should be applied to all cost savings.
- Updated Capital Costs: Capital costs for the final refined ECMs should be updated and added to the financial model. These costs should be reviewed by the engineering team to ensure that all scope has been captured and that pricing components are not redundant. For example, while it is important to capture costs associated with general protection and clean up, these costs should be consolidated for all measures intended to be implemented at the same time, such as during tenant lease turnover. Any allowances and contingencies should be carefully reviewed for applicability. Current contracts with BMS companies should also be reviewed to determine whether controls or sequence of operations upgrades will be charged to the client or are already included in the contract.
While it is important to capture the full extent of the capital costs for each measure, inflated costs run the risk of distorting the final results. This could be the difference between implementing or foregoing a particular ECM. Capital costs for each ECM should be distributed across the implementation timeline as is appropriate. Construction escalators should be applied to all cost estimates to capture the impact of implementing an ECM in the near term vs. toward the end of the study period.
- Repairs and Maintenance Costs: All impacts and adjustments to the current maintenance and repairs budget because of ECM implementation should be accounted for in the financial model. If an ECM is expected to reduce repairs or maintenance costs (e.g., upgrade and replacement of dilapidated equipment, automation of manual processes, etc.) then these incremental savings should be included in the financial calculations. Some ECMs may also increase maintenance costs if they include the addition of new systems or components that require maintenance. These costs and savings should be applied annually as is appropriate.
- Incentives and Rebates: Well-established incentives programs and rebates may also be considered in the financial model. Although these incremental savings are not guaranteed in the future, certain incentives are predictable and reliable enough that they can reasonably be included with low risk. For example, incentives for lighting upgrades are fairly predictable. Specialized incentives programs for new technologies with large carbon reduction potential should be considered as they may significantly improve the financial performance of the measure. For example, studying and pursuing incentives associated with heat pumps may reduce the payback time or improve the NPV of heating electrification measures.
- Carbon Emissions Reductions: Carbon emissions reductions for each ECM under consideration should be included in the financial model. These are direct outputs from the final modeling results from the Energy & Carbon Modeling section. These reductions will be applied according to the implementation timeline, to calculate the annual carbon emissions, cost per ton of CO2, and cumulative carbon reduction impact of each package.
- LL97 Emissions Limits and Other Project Benchmarks: The LL97 building emissions limits for the years 2024-2029, 2030-2034, and 2035 and beyond will be needed to assess projected compliance with the law, and project future fines/fine avoidance for 2024-2029 and beyond. Other significant project benchmarks and objectives should be brought into the review of the final results to compare the performance of each package against these metrics. For example, 40%, 50% and 80% reduction of carbon emissions from a 2005 baseline are common benchmarks.
Activities
- Project Annual Carbon Emissions for All Packages: Annual carbon emissions are calculated by multiplying the annual energy consumption of the building by the associated carbon coefficient for the fuel source. Annual emissions should be calculated for the BAU baseline, as well as for each package under consideration so that these projections can be compared to the LL97 limits and other project objectives.
- Calculate LL97 Fines and Fines Avoided: LL97 fines are calculated by determining the difference between the building’s annual emissions (tCO2e) and the calculated emissions limit for the building (tCO2e) and multiplying the difference by the fee of $268. Therefore, one needs to determine the building’s emissions limits for the applicable years, as well as the projected annual carbon emissions. Annual carbon emissions are calculated by multiplying the energy consumption of the building by the associated carbon coefficient for the fuel source. Fine avoidance can be calculated by using the projected future energy consumption for the building as the proposed ECMs are implemented.
Although building emissions limits can be calculated for the years 2024-2029 and 2030-2034, and an ultimate limit has been included in the law for the time period between 2035 and 2050, carbon coefficients are currently not available for the years 2030 and beyond. While carbon coefficients for fuel sources like natural gas and steam may remain relatively stagnant throughout this time period, the electrical grid coefficient is expected to change as the grid decarbonizes. Until these carbon coefficients are established by the legislation, only projections can be used in their stead.
- Calculate Potential Incentives from IRA programs: The Inflation Reduction Act (IRA) is the greatest investment in US economic growth and climate action in our lifetimes. Passed in 2022, the IRA, paired with the Bipartisan Infrastructure Law (BIL) and other federal policies and initiatives, offers a suite of federal incentives with some aimed at promoting the decarbonization of large buildings. These incentives are designed to encourage building owners to invest in energy-efficient and sustainable technologies, thereby reducing their carbon footprint and contributing to national climate goals. For more information on available or upcoming federal incentives, please visit our federal incentives resource page.
- Calculate NPV for ECMs and Packages: The NPV calculation for each ECM should be revised and expanded to include the updated energy cost savings and capital costs, as well as the maintenance costs, incentives, and the contribution of any LL97 fines avoided. Once the NPV for each measure is calculated, the NPV for each package can be calculated as the sum of all the NPVs of the ECMs included in the package.
- Calculate Additional Financial Metrics: Simple payback for each ECM and package can also be calculated by taking the capital costs, subtracting one-time deductions from incentives, and dividing by the total energy cost savings and other annual savings like maintenance and repairs savings. It is important to note that this simple payback does not factor in the implementation timeline for the measures which may prolong the payback period if it takes several years for the measures to be completely executed. Also important to consider when evaluating the payback for an individual measure is how it compares to the useful life of the proposed ECM. Large paybacks for an ECM should not be discounted if they occur within the useful life of the system. Another useful metric is the cost per ton of carbon dioxide equivalent reduced ($/tCO2e). This can be calculated for each ECM as well as for each package as a whole. This is a helpful metric that can be used to identify which ECMs are particularly effective at reducing carbon given their cost and can be used to refine which ECMs are included in the different packages.
Outputs
- Annual Carbon Emissions for All Packages: The projected annual carbon emissions for all packages should be graphed for each year of the study period. Any relevant project objectives (e.g., avoiding fines under LL97, 80% carbon emissions reduction from 2005 baseline, etc.) should be overlaid on these results to evaluate which packages achieve the stated goals. It may be the case that only some of the packages meet all the project’s carbon reduction objectives. This analysis is important to determine the level of technical intervention required at the building scale.
- NPV vs. CO2 Reduction: The primary financial output of the model will be the NPV value for each package, which can be compared with the associated cumulative carbon emissions reduction over the study period.
Packages with a positive NPV appear to outperform the owner’s rate of return from other investments. Packages with a negative NPV appear to underperform the owner’s expectations for alternative uses of funds. It is important to note that packages with a negative NPV may still show simple payback well within the useful life for the associated investments.
- Techno-Economic ECM Package Recommendation: Based on the above results, the project team should recommend a package for implementation by the client. The owner must decide how close to NPV neutral they want to get compared to maximizing NPV, which does not necessarily lead to CO2 minimization, and weigh these financial considerations with other relevant project goals.
Beyond the NPV for each package, it may be necessary to extract the annual cash flows from the financial model for presentation to the client (e.g., annual capital costs, energy cost savings, incentives, etc.).
The project team should investigate, and the owner consider financial engineering in their decision making. ESCOs or selling and leasing back an ECM can bring cost savings forward in time while reducing the overall cashflow benefits to the owner over a term.
Lessons Learned & Key Considerations
- Energy savings of low-cost measures can offset the cost of other ECMs: In many buildings, improved efficiency, comfort and cost savings can begin well before the final ECM packages are selected, since some measures such as set points, bypass valves and energy management controls can be adjusted at little or no cost as soon as suboptimal performance is identified. Any energy savings associated with these low-to-no cost adjustments should be measured and tracked as they may help offset the cost of other ECMs in the final recommended package.
- Financing is an important piece of the puzzle: Providing the project ownership team with information about different financing options can increase the probability that a project will be implemented. Learn more about different financing mechanisms here.
In Practice
Tags
Insights from Empire Building Challenge
Educating building stakeholders about the benefits of high-performance buildings and creating a skilled operations and maintenance workforce are key to driving holistic energy management and lasting decarbonization. Below are some training resources to help project teams get started.
Online Training and Resources
The NYC Accelerator offers online and in-person trainings on a host of building and energy topics, including building energy law compliance, decarbonization strategies, and building systems. Visit the NYC Accelerator website to access 30+ training courses.
Urban Green Council (UGC) is committed to training architects, engineers, building owners and managers, tradespeople and other professionals in the latest developments and best practices for creating and maintaining sustainable buildings. They offer the following resources:
- GPRO: A comprehensive national training and certificate program for trades and contractors. Courses include Operations and Maintenance, Plumbing, Electrical Systems, Construction Management and HVACR.
- Energy Code Training: Essential training on how to comply and get the most out of New York State and NYC’s energy code for architects and engineers.
- Cross-Learning Alliance: UGC has joined with AIA New York and the New York Chapter of ASHRAE to launch the Cross-Learning Alliance. Alliance programs are designed to bridge the knowledge gap between the people that own, design, build, manage, operate and commission buildings.
- Resource Library: Browse through UGC’s research reports, event recaps, blog posts and more.
Workforce Development and Training
Workforce development and training are essential components to creating a robust, green economy. To meet the requirements of a clean energy economy as outlined in the Clean Energy Fund (CEF) and the Climate Leadership and Community Protection Act (Climate Act), NYSERDA has dedicated more than $100 million in funding to support clean energy workforce development and training. Support is available in six separate categories:
- Training for building and operations staff to properly operate and maintain building systems.
- On-the-job training for new clean energy workers.
- Internships for students looking to gain hands-on skills at a clean energy company.
- Curriculum development to meet the demands of clean energy employers.
- Creation of a sustainable talent pipeline that can reduce the business cost of hiring new workers.
- Career pathways training for high-efficiency HVAC and heat pumps.
Property owners and facility managers interested in improving their team’s energy management knowledge and skills can access funding for training through NYSERDA’s Building Operations and Maintenance Workforce Development Training Program. NYSERDA can fund on-site trainings, apprenticeships, internships, and more.
Tags
The Funding and Incentives Resource Hub can help you navigate and discover the many rebates, funding opportunities, and other incentives including those available through the Inflation Reduction Act and Bipartisan Infrastructure Law. This new hub will continue to evolve as we add resources as they become available*, so be sure to check back frequently. You can refine your search by sector, technology, source, and type using the filters below.
Tags
New engineering design means and methods are needed to enable and accelerate adoption of low-carbon retrofit technologies. Efficient heating and cooling energy systems are widely available but underused due to lack of knowledge and thermal system interaction.
Decarbonization requires adapting distribution systems designed for legacy thermal supply to electric and renewable thermal energy systems. New design strategies are emerging which can help alleviate space constraint issues, provide peak thermal capacity, optimize operational efficiencies, utilize waste heat, and reduce the need for oversized, electrified thermal energy systems creating retrofit cost compression. The latest research on thermal energy networks focuses on utilizing heat and cold more sustainably by creating innovative components and control strategies for thermal systems.
In this Empire Building Challenge webinar, Cary Smith and Garen Ewbank from The GreyEdge Group provide perspectives on designing efficient thermal networks for decarbonization. The recorded discussion focuses on low temperature distribution, electrification with advanced heat pumps, thermal storage integration, and thermal interactive buildings.
The materials below were part of a presentation given on Jun 18, 2020, as part of the Empire Building Challenge, in partnership with the GreyEdge Group.