Insights from the Empire Building Challenge
A calibrated energy model should play a central role in building out a decarbonization plan because it provides insights on:
- Current building energy and carbon profiles, and costs.
- Potential energy, carbon, and cost savings of energy conservation measures (ECMs.
- The impact of groups of ECMs, and the order of implementation and timeline.
The steps to follow include:
- An initial energy model is developed using commonly available building information such as architectural floorplans, MEP schedule sheets, and BMS sequences of operation.
- The initial model is then refined and “calibrated” to the building’s real utility data for each utility consumed, creating a baseline condition that ECM’s will be compared against.
- The baseline energy model is used as a test bed for individual ECMs to understand potential energy, carbon, and cost impacts.
- Evaluate the financial performance of each ECM. These results will be used to identify strategies that are economically viable and should be considered further.
- Those ECMs that are economically viable on their own may be grouped together with other ECMs to help build a holistic business case for system optimization and maximum carbon reduction.
- During the evaluation process, the project team should take the evolving emission factors associated with utilities such as electricity and steam, as well as the impact of rising average and design day temperatures/humidity, into account.
Key outputs from the energy modeling workflow should include data driven charts showing energy end use breakdown and costs, carbon footprint of each utility, building carbon emissions vs. LL97 targets and fines, and who “owns” the carbon footprint (i.e. tenants, building operations). It is important to note that not all energy models are created equally. For a deep energy retrofit project, the accuracy of the energy model should align with ANSI/ASHRAE/IES Standard 90.1. Code or LEED energy models that were developed for the building in the past are not appropriate for this effort.
Learn more about building energy modeling.
Below is a selection of the energy modeling software packages used to support the case study findings presented in this Playbook, and throughout the industry.
1. Build and Calibrate the Initial Energy Model
An energy model is developed in multiple phases. In the first phase, the energy modeler must build an initial model that captures the geometry, material attributes, occupancy types, MEP systems and basic information about the building’s operations. The energy modeler should also include surrounding buildings that may impact sun exposure on the different facades of the building under study. This initial model will produce a rough estimate of how the building performs every hour during the year. Then in the next phase, the energy modeler must hone the model’s accuracy by “calibrating” the initial model to utility data and detailed building operations information. Code or LEED energy models that may have been created for the building during its initial design and construction should not be used in deep energy retrofit study efforts because they do not reflect the actual performance of the building under study.
Lessons Learned and Key Considerations
- Determine energy model accuracy expectations early: Energy model accuracy can vary widely. For a deep energy retrofit study, the energy model should be highly accurate and align with ANSI/ASHRAE/IES Standard 90.1. Building management teams should set model accuracy expectations with the energy modeler at the onset of the project. This will help inform how assumptions are made and where the modeler should or should not simplify certain aspects of the model.
- Energy model calibration takes time but is worth the investment: Calibrating the initial energy model is a continuous and iterative process that can span multiple days or weeks depending on the complexity of the building. This time investment is well worth it because the quality of the energy modeling results is directly dependent on the quality of the calibration effort.
- Sync energy modeling assumptions with site observations: Even well-maintained buildings with stringent base-building and tenant standards have operational nuances and anomalies. Equipment may be shut off or sequences may be manually overwritten because the system wasn’t commissioned, wasn’t correctly integrated with the BMS, or was causing a localized issue that required a quick fix. This is especially true for older existing buildings that have had operations team turnover resulting in a loss of institutional knowledge over the years. For the energy model to accurately capture savings for ECMs, the calibrated model must reflect real-life operation. The project’s energy modeler should capture these nuances in the calibrated model whenever possible.
- Perfection is the enemy of “good enough”: The energy model will never perfectly simulate the performance of the building. There will also be a margin of error that comes from very specific nuances in building construction or operation that can’t be captured by simulation-based software. The project team should set reasonable expectations for the level of modeling and calibration effort that aligns with AANSI/ASHRAE/IES Standard 90.1 but also conforms to the project schedule and status.
- Share model visualization with the project team: Energy modeling can be a complex topic that may seem inaccessible to non-technical audiences. To maintain good project team engagement during the energy modeling phase, the energy modeler should prepare and share data visualizations that can help tell the story of how the building uses energy. Graphs, rendering, and infographics are great examples of visual assets that can demystify the energy modeling process.
2. Create the Baseline Energy Model
The baseline model represents the current systems and operations of the building, adjusted for “typical” weather conditions and other criteria. Energy savings for all proposed ECMs will be calculated relative to the baseline model performance.
Inputs
- The calibrated energy model
- TMY weather data
- List of planned upgrades, tenant lease turnover schedules
Activities
Make Necessary Adjustments to the Baseline Model: To create a baseline energy model, the calibrated energy model consumption should be adjusted to account for the following:
- Weather: Typical weather data for the site can be modeled using TMY3 data files, which capture and compare typical performance and eliminate any extreme weather event effects that may have occurred in the baseline year. TMY3 files are produced by the National Renewable Energy Laboratory and can be freely accessed and downloaded from the EnergyPlus website.
- Occupancy (Lease Turnover or COVID): The baseline energy model should be adjusted to account for any fluctuations in building occupancy that are expected to occur over the study period. For example, tenant lease turnover schedules should be collected during the Discovery Phase and accounted for in the baseline model. Similarly, any disruptions to building occupancy, such as those experienced during the COVID 19 global pandemic, should be captured in the baseline model. To understand the full magnitude of ECM impacts, it is important to separate energy reductions resulting from ECMs versus those resulting from lower occupancy levels.
- Planned Upgrades: The baseline model should be adjusted to account for any planned projects that will impact the building’s energy consumption. By capturing these savings in the baseline model, the project team will avoid projecting ECM savings that are no longer available because they have already been captured by planned projects.
The baseline model represents “business as usual” building energy consumption and associated energy cost. It is the reference point used to determine the energy savings of potential ECMs and track progress towards reaching project objectives.
Generate Detailed End-Use Breakdowns: Once the baseline energy model is complete, the project team can begin to gain additional insight into how the building uses energy. A particularly useful output of the model is a detailed end-use breakdown like the one shown below:
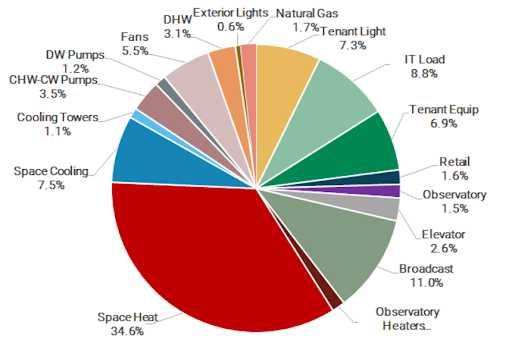
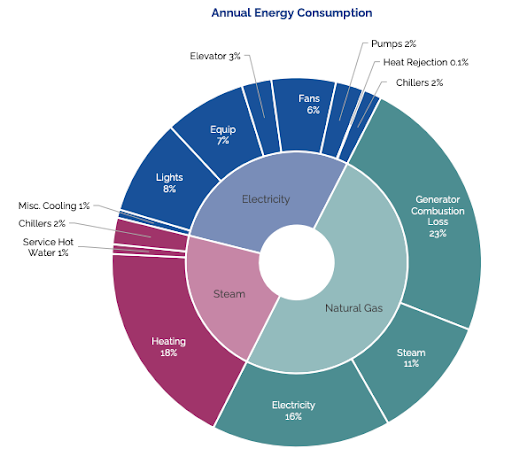
The energy modeler will be able to analyze this end use breakdown and identify systems that appear to be high energy consumers. Hypotheses should be vetted by the engineer and facilities team based on their understanding of the building.
Document Assumptions and Review Initial Results with the Team: After the initial baseline model has been built, the energy modeler should review his/her/their assumptions and the resulting load breakdowns with the project team. The modeler should then solicit feedback from the engineers and building operators who have greater insight into the current building operation and systems design. Feedback should be incorporated into the next iteration of the baseline model. The feedback loop between the energy modeler and the building team will be an iterative process that will continue throughout the duration of the project as more information is collected from the building.
Overlay Carbon Emissions: Once the baseline energy consumption results are refined, the associated operational carbon emissions can be calculated by multiplying the annual energy consumption by a fuel-specific carbon coefficient. Carbon coefficients represent the greenhouse gas emissions intensity of different energy sources and are used to determine a building’s total greenhouse gas emissions in tons of CO2 equivalent. This analysis will identify the primary contributors to greenhouse gas emissions in terms of fuel type, system, and ownership (end-user that is driving the demand).
Refine the Preliminary List of ECMs: At this point, the energy modeler and engineer should work together to refine the preliminary list ECMs that was developed in the “Build the BAU Base Case” task. The additional information gleaned from the detailed end use breakdown should be used to validate the initial list of measures and to identify new areas of focus that were not identified in early phases of the project.
Outputs
Deliverables from the baseline energy model work include the following:
- Baseline energy model is a reference for potential energy, carbon and cost savings
- Building energy consumption and detailed end use breakdowns
- Documented baseline system assumptions
- Finalized List of ECMs for study in the energy model
Lessons Learned And Key Considerations
- Document and review input assumptions: A robust energy model can be a reusable tool that can serve the building team for many years after the initial deep energy retrofit study. To ensure the information within the model is accurate and up to date, any inputs and assumptions should be documented and shared with the building management team. This will give the team the opportunity to correct any assumptions that do not align with the actual operation of the building and will create a log where inputs can be revised and updated as the building evolves.
3. Analyze Individual ECMs
In this task, the energy modeler will run all ECMs in the energy model and extract associated energy, carbon, and cost savings for each. For this task, the energy modeler will need the baseline energy model and the finalized list of ECMs that will be evaluated.
Inputs
For this task, the energy modeler will need the baseline energy model and the finalized list of ECMs that will be evaluated.
Activities
Develop a Modeling Strategy for Each Energy Conservation Measure (ECM): Before the modeler begins modeling each ECM, he/she/they should develop a modeling strategy for each measure including performance characteristics and any important assumptions. Documenting model inputs and modeling strategy for each ECM will make it easier to troubleshoot if there are any surprising results.
Run ECMs in the Model and Analyze Results: Once all ECMs are explicitly defined and the modeling strategy has been finalized, the modeler will run each ECM to create a proposed energy model. The proposed energy model is compared to the baseline energy model to estimate energy, carbon and cost savings. The energy modeler will extract savings for each ECM from the proposed model, which will enable the team to study the individual impact of each ECM and vet the results. Energy savings for individual ECMs should be compared to industry experience to gauge their validity. When surprising results arise, the team must explore why and either justify the inputs or modify them according to additional information.
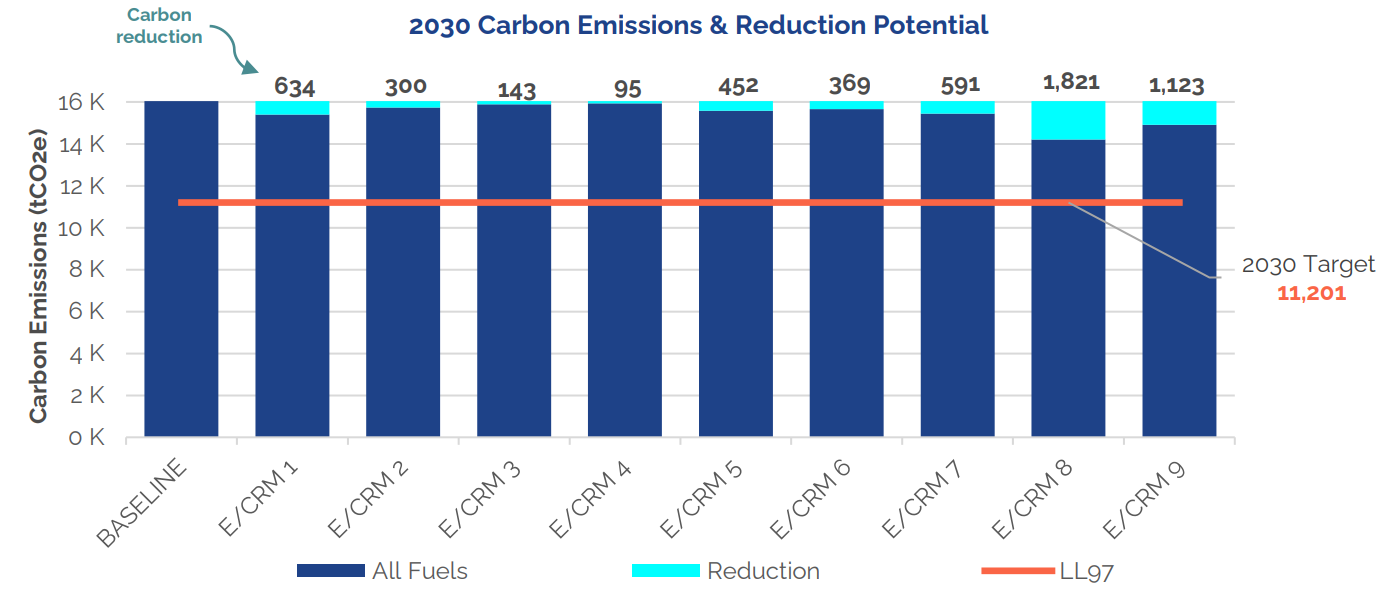

Refine and Troubleshoot as Needed: Assumptions may need to be revised after this initial review of the results, especially if there are unexpected results.
Compare Mutually Exclusive ECMs: In some cases, the team may develop mutually exclusive ECMs. These competing ECMS must be compared to determine which is the most energy efficient and by what margin. The energy model can be used to run multiple ECM options and compare estimated energy savings between them. The project team should decide which mutually exclusive ECMs should be advanced into the future rounds of analysis before packaging ECM in the next phase of modeling.
Assess Maximum Theoretical Potential for Energy Savings: The final energy consumption of the proposed model will factor in all the energy savings associated with the ECMs. This resulting value is the theoretical minimum energy consumption for the building, assuming all technically viable ECMs are implemented. At this point it is helpful to determine the percent reduction from the baseline and evaluate how this theoretical minimum stacks up to the project objectives. Important questions to answer include:
- Does the theoretical minimum energy consumption meet or exceed the project’s energy and carbon goals, and if so by how much?
- Which ECMs contribute most significantly to energy and carbon reductions and are they likely to be financially feasible?
- Are most of the energy savings attributable to a few select ECMs or are energy savings spread evenly amongst many small measures?
The analysis of the energy modeling results can be facilitated by the creation of ECM waterfall charts which show the baseline energy consumption / carbon emissions and the progressive impact of each ECM on these values. The final energy consumption and carbon emission of the proposed model will establish the theoretical minimum.
Outputs
Outputs and deliverables of this work include:
- Initial energy, carbon, and cost savings for individual ECMs. Based on this initial review and analysis, the team will identify further data collection required to refine the modeling assumptions and improve the accuracy of the outputs.
- Actionable information regarding which mutually exclusive ECMs are most impactful and should be advanced to the next phase of modeling.
- The maximum theoretical energy savings and carbon reduction for the building. This will give the project team an indication of how many ECMs may need to be implemented to meet the project objectives.
- Initial energy cost savings for each measure, which can be used to inform preliminary financial analyses.
Lessons Learned & Key Considerations
Review and question surprising results: When reviewing preliminary energy savings, it is important to make sure that the results make sense and question any surprising results. The energy modeling results are only as accurate as the modeling inputs. These assumptions must be vetted to ensure accurate savings. Data collection during this time will be useful to determine modeling assumptions. Assumptions can also be informed by the insights and advice from industry experts. Energy modeling is an iterative process, and the model will continue to be refined as more information is collected.
Identify high priority ECMs: Preliminary results may indicate that most of the energy savings available are attributable to a select number of ECMs. Implementing these select few ECMs may be all that is required to meet the project’s short-term objectives. The project team should focus on refining the inputs for these high impact ECMs to ensure accurate savings.
Remember many small measures have a cumulative impact: To maximize savings and meet long-term project objectives like 80×50 it is likely that a wider array of ECMs will need to be considered for implementation. This holds true especially for buildings that have undergone recent renovations where the most impactful ECMs have already been executed. In this case it may be necessary to evaluate the cumulative impact of many small measures. Therefore, individual measures with minor carbon reduction impacts should not be dismissed too quickly.
4. Group, Sequence, and Package ECMs
As the Energy and Carbon Modeling phase is progressing, a preliminary financial analysis of individual ECMs will also take place in parallel. Preliminary results from the financial analysis will help inform this phase of modeling. Individual ECMs should not necessarily be discarded based solely on their associated capital cost; expensive ECMs can be grouped together with related financially viable measures to optimize savings and make a more comprehensive business case that maximizes CO2 reduction while still addressing investment return hurdles.
Once ECMs have been grouped, an implementation duration and timeline should be established for each. This will depend on factors like short term project budgets, tenant lease turnover, operational budgets, and maintenance schedules. The ECMs should then be sequenced according to their implementation timeline so that energy savings for each ECM can be captured accordingly.
Finally, several ECM packages should be assembled for owner evaluation. Each package will include a different combination of ECMs to be implemented with varying degrees of cost and carbon impact. This variety will provide the owner with options to choose from when striving to balance the project objectives and constraints.
Inputs
For this task the project team will need the following inputs:
- Energy, carbon & cost savings from the proposed energy model
- Preliminary ECM capital costs estimates: Preliminary results from the financial analysis will provide approximate NPV values for each ECM based on the projected energy cost savings and capital costs. These results will be used to identify those ECMs that are economically viable on their own, those that are worth pursuing due to large carbon impact, and those that should be discarded at this point due to technical infeasibility, cost, or low carbon impact. Those ECMs that are economically viable on their own may be grouped together with related, and costly, but effective, ECMs to help build a stronger business case.
Outputs
Outputs and deliverables of this task include the following:
- Finalized grouped and sequenced ECM list.
- Results from Packaged ECMS for Owner consideration.
Activities
Establish the Final List of ECMs: Once a preliminary financial analysis has been conducted and approximate NPV values and energy and reductions are calculated for each ECM, the list of measures should be reviewed and finalized. Typically, ECMs will fall into the 5 categories described below, with associated outcomes:
- ECM has a positive NPV and has a large carbon impact. ECM should be considered seriously for implementation. Additional QA/QC should be completed to ensure savings are accurate.
- ECMs that has a positive NPV but has a minor carbon impact. ECM should be evaluated collectively with other measures, as the impact of many small measures can compound.
- ECM has a positive NPV and has a large carbon impact but is technically challenging or infeasible. ECM should likely be eliminated because it will not seriously be considered for implementation by the Owner or building operations team
- ECM has a negative NPV (simple payback may still be within the useful life of the ECM) but has a large carbon impact. Financial case for the ECM should be investigated further – the incorporation of maintenance costs, baseline requirements or planned capex unrelated to emissions reductions, and potential incentives in the financial model may improve the financial performance.
- ECM has a negative NPV and a small carbon impact. ECM should be eliminated.
Group and Sequence the ECMs: Once the list of ECMs has been finalized, the project team should determine the anticipated duration of time required for completion and the implementation sequence. There are various considerations that should be understood during this part of the modeling process:
- The timing of implementation will be unique to each building and vary depending on the types of existing systems and their age and performance. Well maintained systems may be able to be updated and optimized in the short term and replaced in the long run depending on the project objectives.
- The sequence of ECMs will depend on various factors including tenant lease turnover schedules, maintenance schedules, and investment cycles.
- Interrelated and codependent ECMs should have the same timeline and/or be sequenced appropriately. Some ECMs should be considered as a group to help make a financial case for optimized carbon reductions.
- The impact of the ECMs will decrease as the sequence progresses, and savings will be less than if they were directly compared to the initial baseline. This is because as each new ECM is executed and absorbed into the baseline model, this “new” baseline model against which new ECMs are compared performs more efficiently, thereby decreasing the potential for savings.
Create ECM Packages: Once the ECMs have been sequenced, various implementation packages should be compiled for final evaluation. Given that implementing all ECMs will likely be cost prohibitive, the project team should provide the owner with different options along the spectrum of project cost and carbon reduction.
To book end the problem, it is recommended that two of the proposed packages be a “CO2 Maximum Reduction” package and an “NPV Maximum” package. These packages are described below:
- CO2 Maximum Reduction: Package includes all technically viable measures, even if they are not economically viable at the time of the analysis. The purpose of this package is to find the technical maximum CO2 reductions achievable.
- NPV Maximum: Package includes only those measures that payback within the study period and have positive NPVs. These are the minimum CO2 reductions that can be expected with a financially viable package.
Additional packages should be created and evaluated based on feedback from the project team. These hybrid packages will allow the owner to choose from a wide range of options with different value propositions.
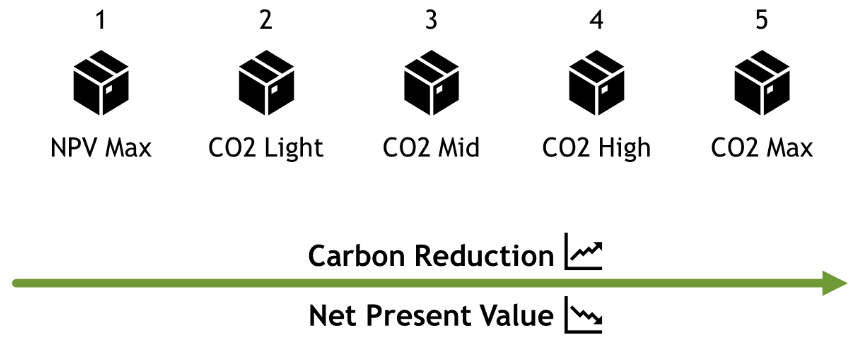
Lessons Learned & Key Considerations
Visualize the results: A helpful tool for analyzing ECMs results is a 2 x 2 matrix that shows the NPV vs. the CO2 reductions for each ECM.
Consider non-energy benefits: Before eliminating measures because they have small carbon impacts, the project team should evaluate the non-energy benefits of the measure. If the non-energy benefits align with the owner’s overall sustainability strategy or make the building a more valuable asset, the building team may still wish to pursue the item. For example, a façade upgrade or replacement may not have a positive NVP but will make the building more competitive with newer buildings.
5. Generate a Decarbonization Roadmap
Once the finalized ECMs have been grouped, sequenced, and packaged, the energy model can be run to obtain final results. These results will be used in the detailed financial analysis and will represent a time-dependent decarbonization roadmap for the building. The final results will include energy savings, energy cost, and CO2 reduction for each package under study, and should phased according to the anticipated implementation timeline to reflect the gradual and overlapping impacts of each measure over a 20- or 30-year time horizon. CO2 reduction over a longer time horizon should include a changing electric grid carbon coefficient to account for grid decarbonization.
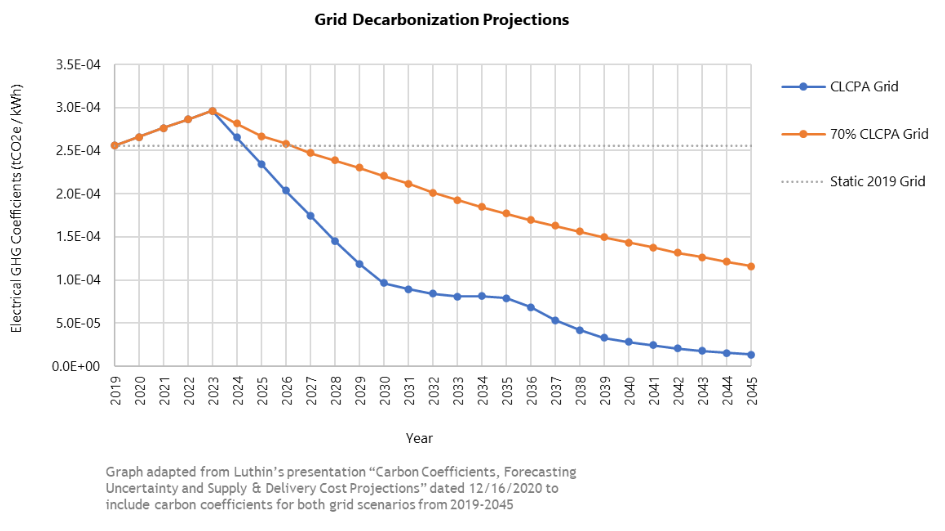
Inputs
The inputs for this task include:
- The finalized ECM Packages
- Carbon coefficients for the Future Grid
Activities
Run Final ECM Packages in the Model and Analyze Results: The modeler should update the proposed model based on the final list of ECM packages and intended implementation sequence. Energy results should be provided for each ECM, even if there are several ECMs that are intended to be grouped together, as this provides granular data for the financial analysis to be conducted down the line. This is important because each ECM may have distinct capital costs, maintenance costs, and incentive implications which may impact the financial viability of the measure.
To reduce the modeling time, it may be assumed that a given ECM’s savings are recognized at once, even if it is anticipated that the ECM and associated savings will be realized over a period of several years. These savings can be split proportionally according to the intended timeline in a post-processing exercise without a major impact on the results, so long as the sequence of the ECMs is correct.
Calculate Savings from the Baseline: The final run of the proposed energy model will produce energy, carbon and cost information that should be compared to the baseline energy model to determine anticipated savings. During this exercise, project teams should consider the following:
- The energy model provides energy costs for each run, but it may be beneficial to conduct advanced tariff analysis that evaluates the anticipated annual hourly energy consumption for each package. Given the energy consumption results from the model, and the implementation timeline, a composite file of hourly data can be created to accurately reflect the percentage of each ECM that has been implemented each year. This will result in an energy consumption profile that reflects the expected annual peak and associated demand charges. More accurate utility costs can be calculated using this information. At a minimum, a utility cost escalator should be applied to the initial calculated energy cost savings to capture the impact of changing rates over time.
- The anticipated CO2 emissions reductions associated with each ECM can be calculated by overlaying today’s carbon coefficients onto the energy savings results. For a greater level of accuracy, the carbon coefficients from LL97 can be overlaid on the annual energy consumption for the years where this data is available (2024-2029). Beyond 2029, project teams should consider different electrical grid decarbonization projections and overlay evolving carbon coefficients on the yearly energy consumption. For example, New York’s Climate Leadership and Community Protection Act (CLCPA) targets 70% renewable energy by 2030. Assuming the grid meets the goals and schedule of the CLPCA, the carbon coefficient for electricity for the year 2030 will be much lower than it is today.
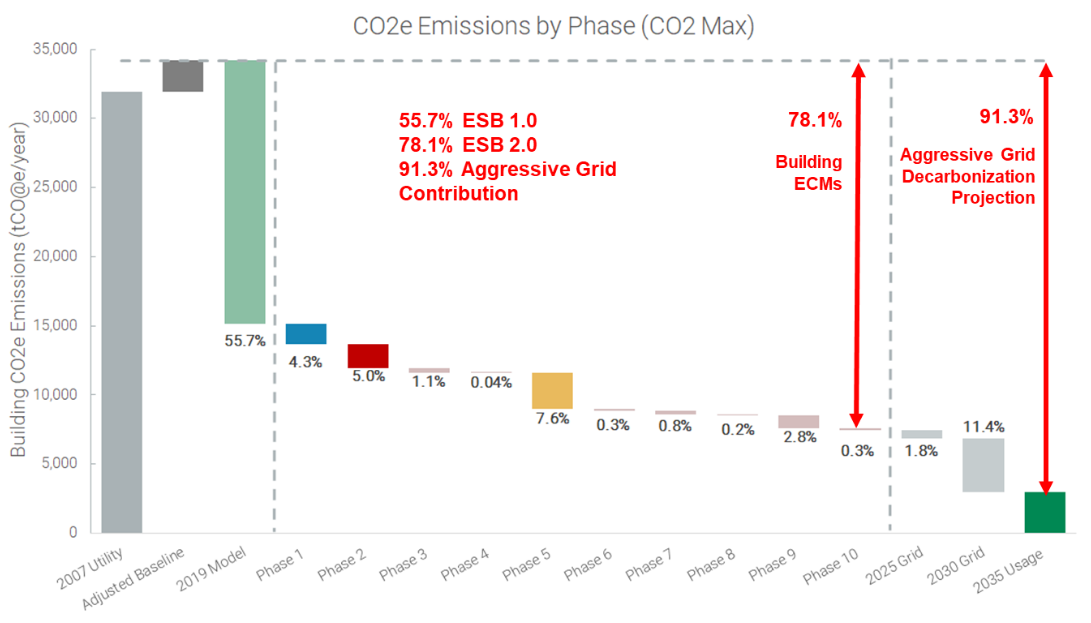
Outputs
The final energy modeling results should include energy savings, energy cost savings, and CO2 reduction for each ECM package studied.
Lessons Learned & Key Considerations
Total carbon emissions depend on the building and the grid: While building owners have control over how efficient their building is, they cannot control the long-term decarbonization of the electrical grid. Building owners can and should evaluate how they can optimize the energy performance of their building through the implementation of ECMs, but the total associated carbon emissions produced by the building will depend on both the magnitude of the energy consumed and how carbon-intensive the source of energy is. For this reason, it is beneficial to understand how different grid scenarios and emissions factors impact the ECM results. A cleaner grid in 2030 may be the difference between meeting or exceeding the LL97 emissions limit for that year.