Fully occupied mixed-income property pursues facade retrofit
Tags
The Heritage, preserved by L+M, showcases a multifamily retrofit project that eliminates fossil fuel usage, improves resident comfort, and minimizes occupant disruption through the use of innovative retrofit methods, materials, and technology. The 34-story, three-building complex , which was built in 1974 next to Central Park in New York City, contains 600 housing units, of which 402 are affordable, with 134 set aside for the formerly unhoused.
The Heritage is an affordable housing development with poor insulation and high utility costs due to outdated heating and water heating systems. This project dramatically cuts heating and cooling needs thanks to major building envelope improvements. Packaged terminal heat pumps for heating and cooling will reduce energy use and costs from the current electric resistance heating system. The retrofit project also pilot-tests state of the art heat pump water heaters and electric laundry dryers.
L+M is a pioneer in mixed-income, market-rate, and mixed-use developments that revive and transform neighborhoods. The company has acquired, built, or preserved nearly 46,000 residential units and more than 1.2 million square feet of retail and community facility space, representing approximately $16.5 billion in development and investment.
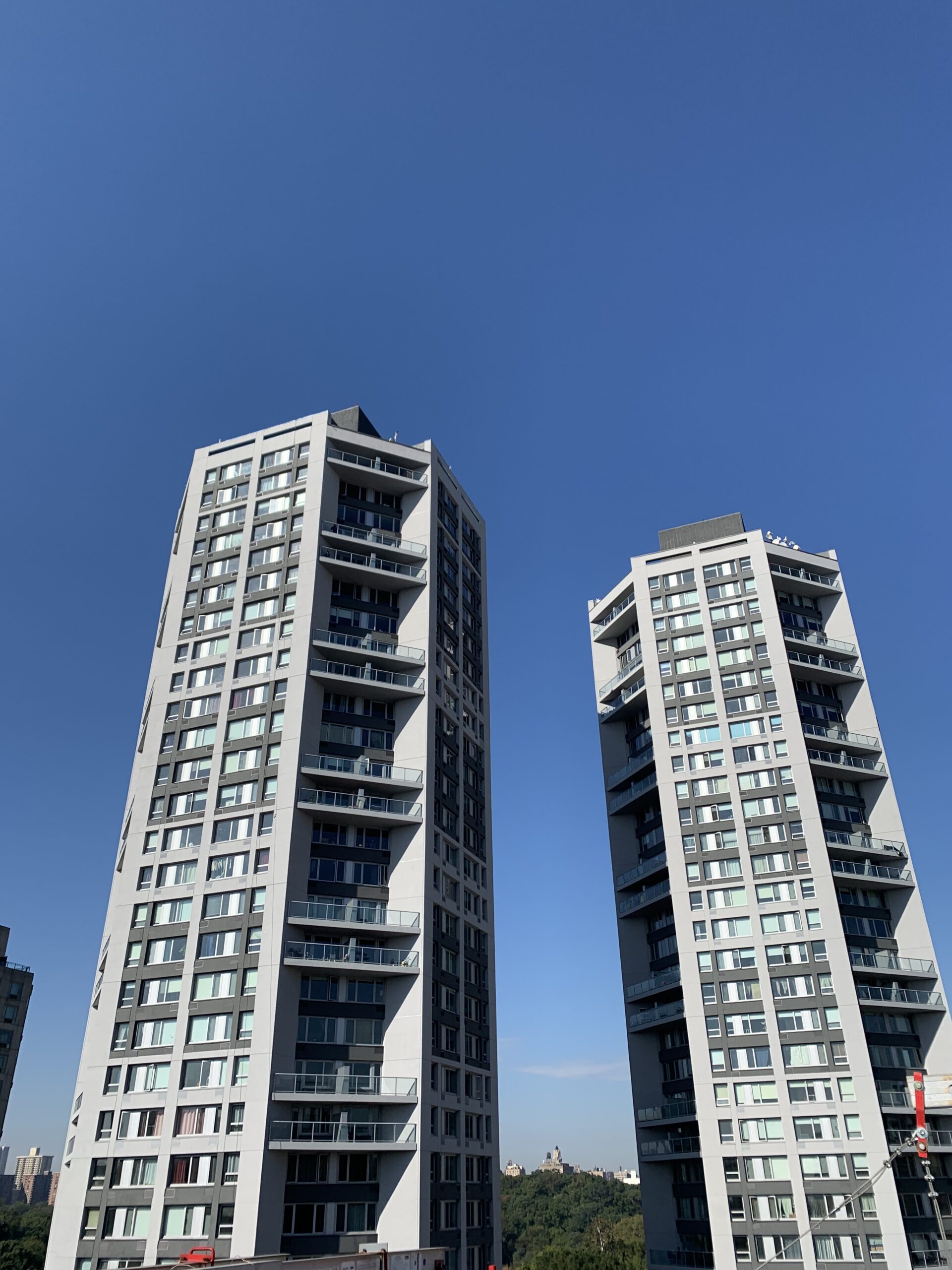
Project Highlights
Step 1
Step 1: Examine Current Conditions
A baseline assessment is key to understanding current systems and performance, then identifying conditions, requirements or events that will trigger a decarbonization effort. The assessment looks across technical systems, asset strategy and sectoral factors.
Building System Conditions
- Equipment nearing end-of-life
- Comfort improvements
- Indoor air quality improvements
- Facade maintenance
- Efficiency improvements
Asset Conditions
- Repositioning
- Recapitalization
- Capital event cycles
- Carbon emissions limits
- Owner sustainability goals
Market Conditions
- Technology improves
L+M takes advantage of the recapitalization cycle of The Heritage to upgrade its infrastructure and include decarbonization measures to meet its climate goals while improving tenant comfort. The property’s age and outdated design made it an ideal candidate for a deep carbon reduction project, focused on envelope improvements, high efficiency heat pumps, and an integrated design approach to minimize tenant disruption. One element of this project is improving views through larger windows.
Step 2
Step 2: Design Resource Efficient Solutions
Effective engineering integrates measures for reducing energy load, recovering wasted heat, and moving towards partial or full electrification. This increases operational efficiencies, optimizes energy peaks, and avoids oversized heating systems, thus alleviating space constraints and minimizing the cost of retrofits to decarbonize the building over time.
Existing Conditions
This diagram illustrates the building prior to the initiation of Strategic Decarbonization planning by the owners and their teams.
Click through the measures under “Building After” to understand the components of the building’s energy transition.
Sequence of Measures
2022
2023
2024
Building System Affected
- heating
- cooling
- ventilation
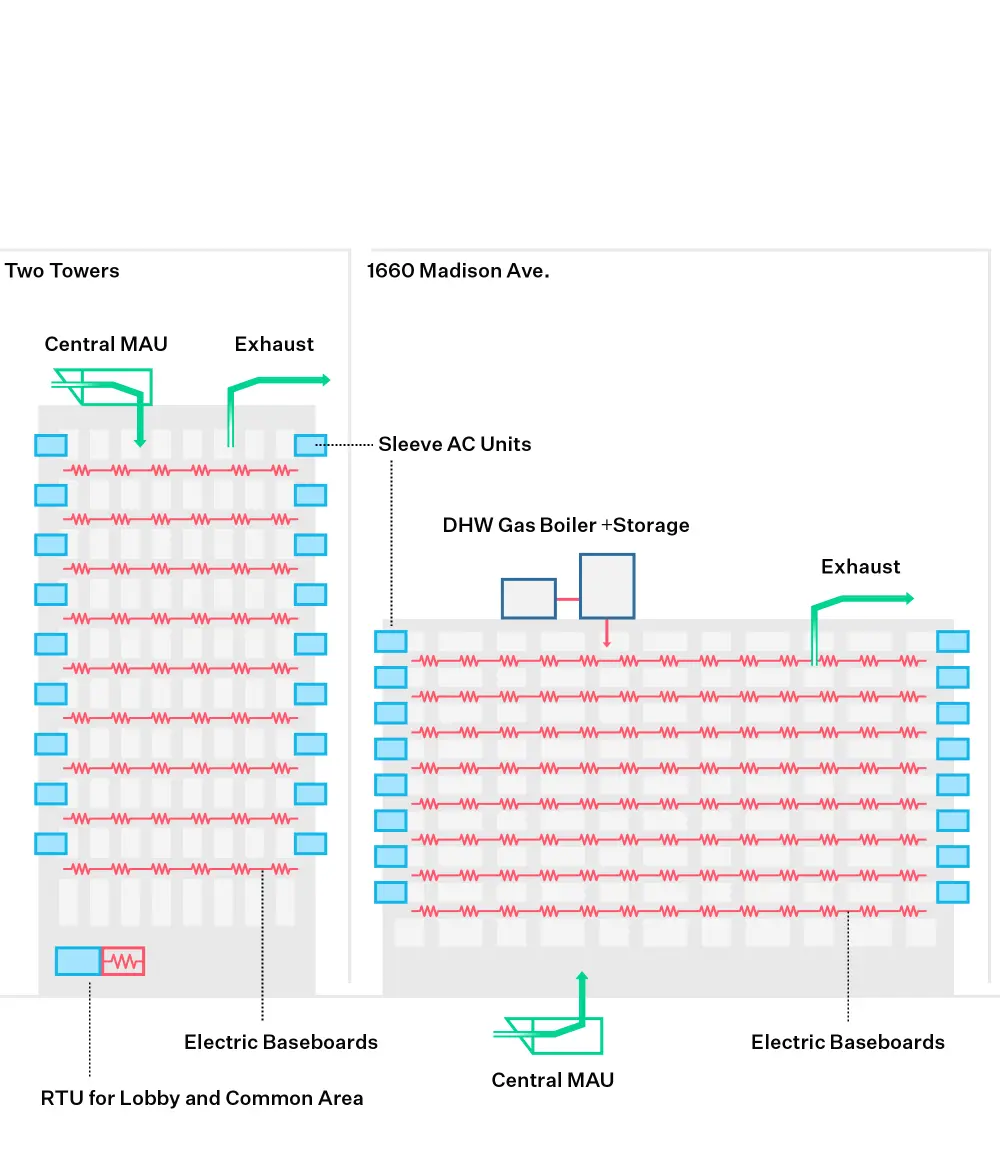
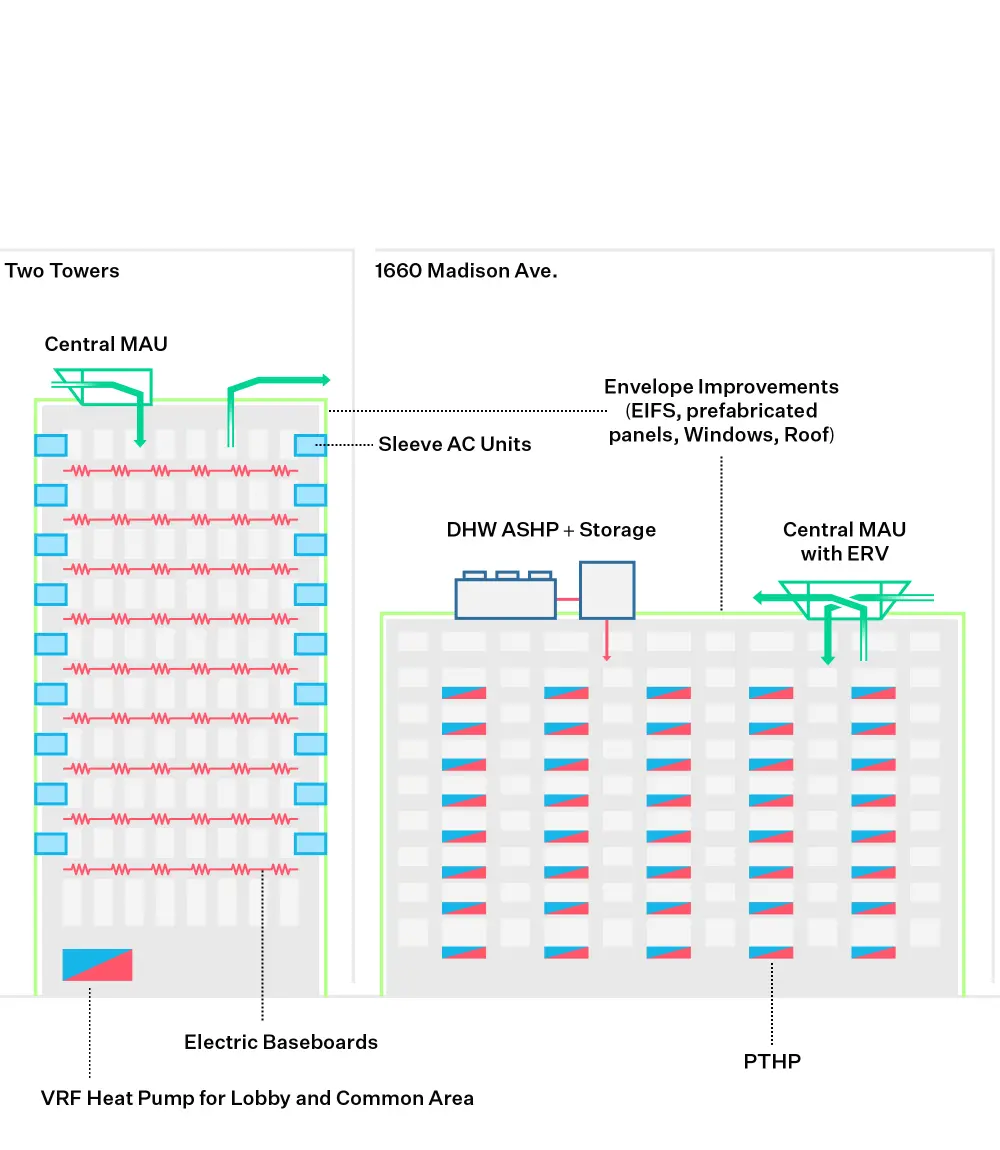
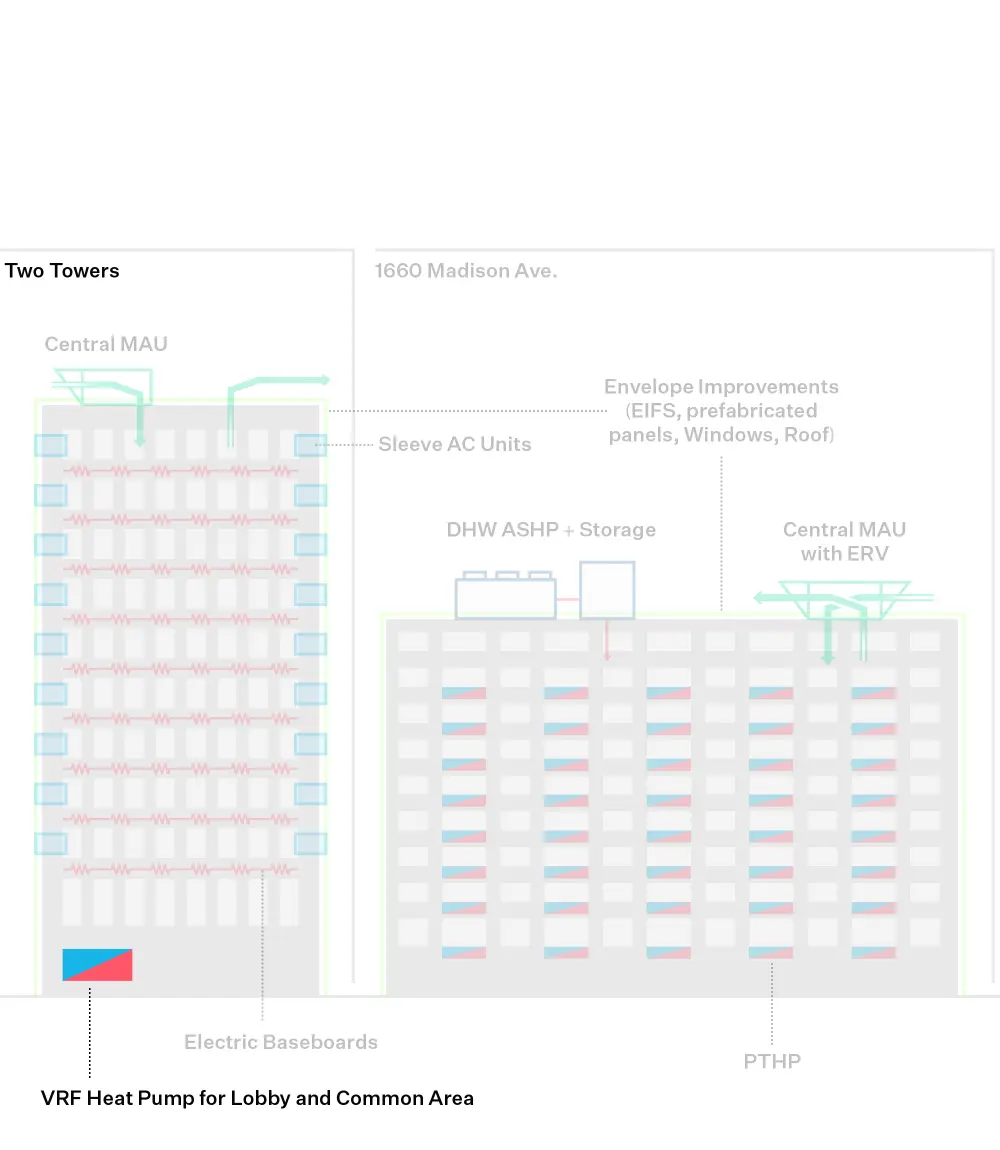
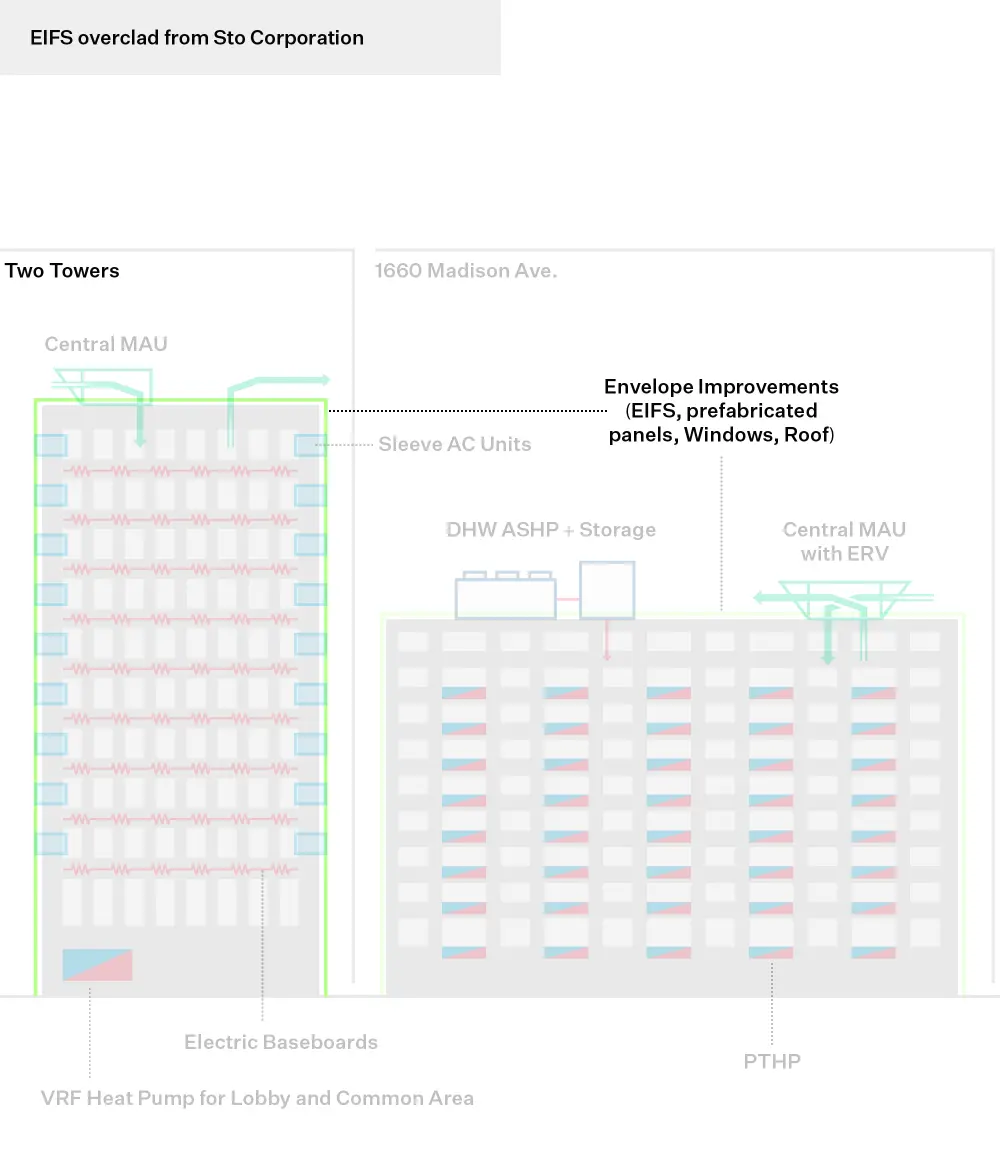
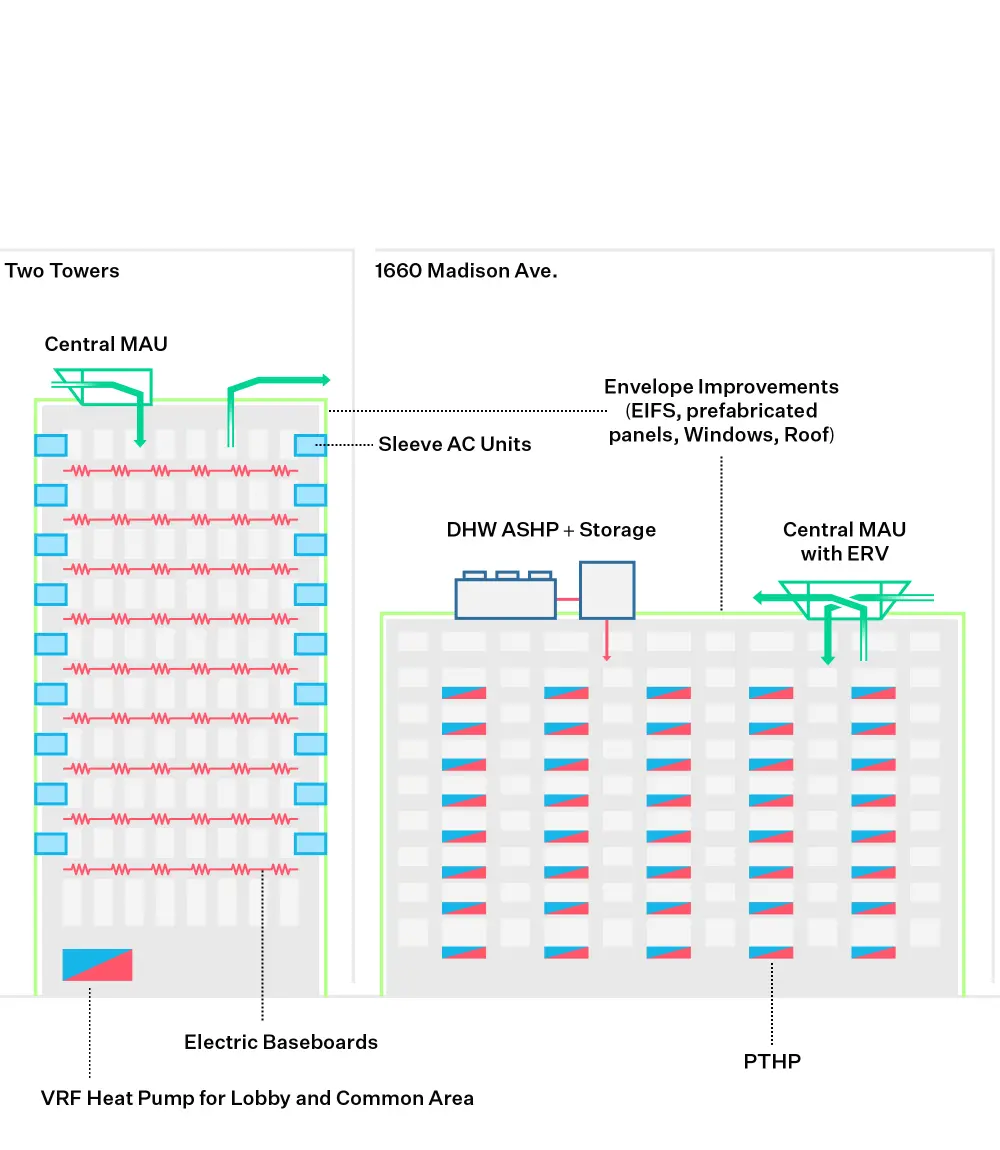
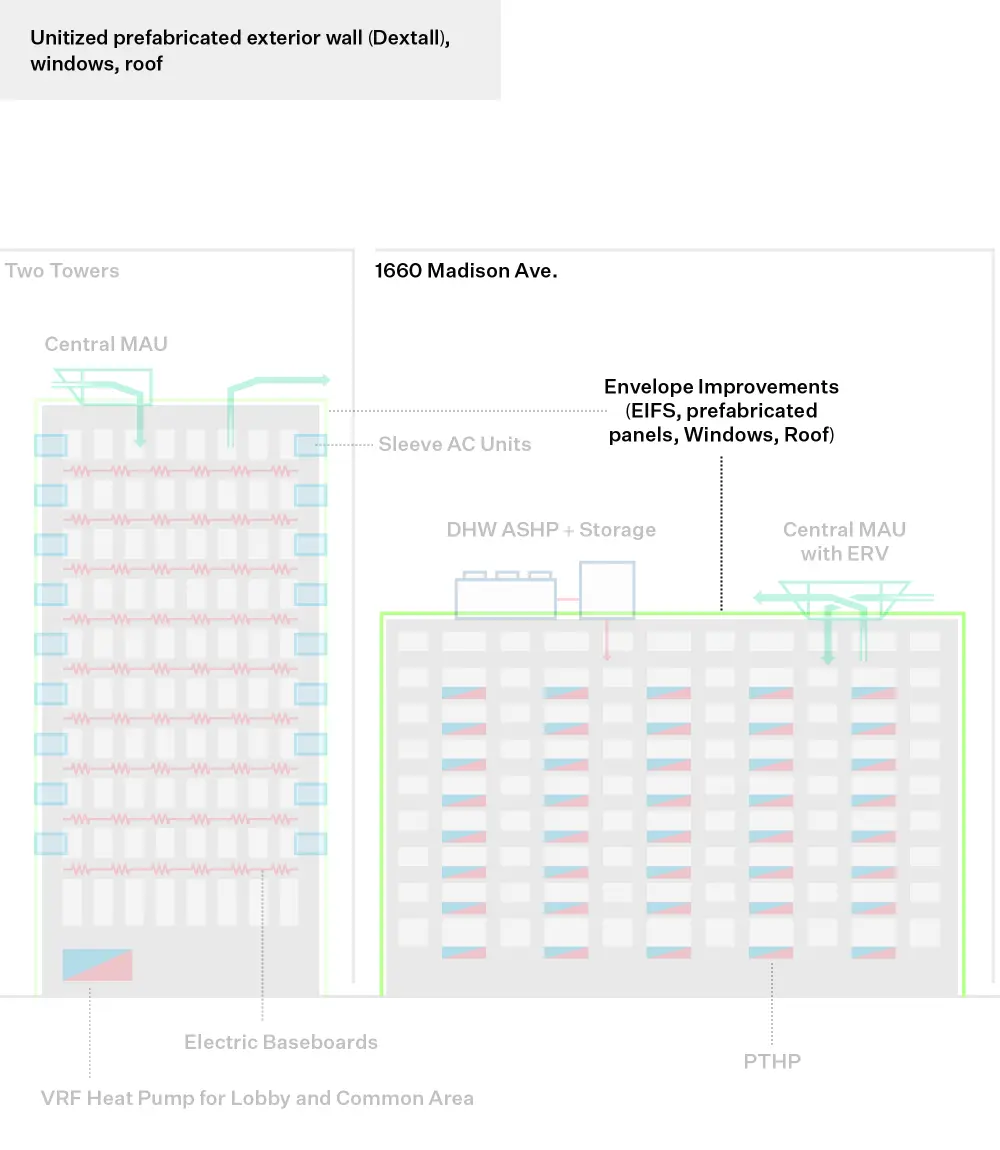
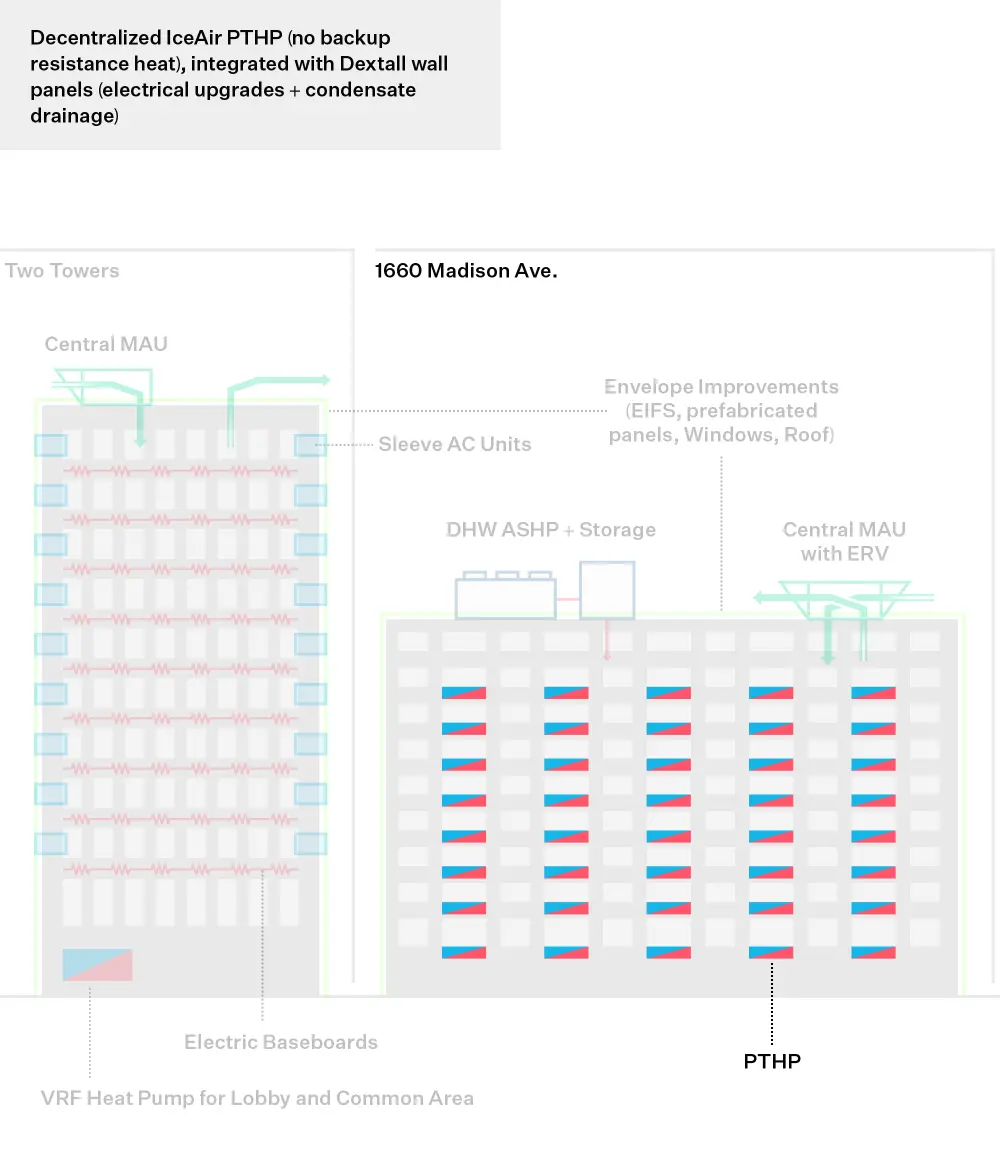
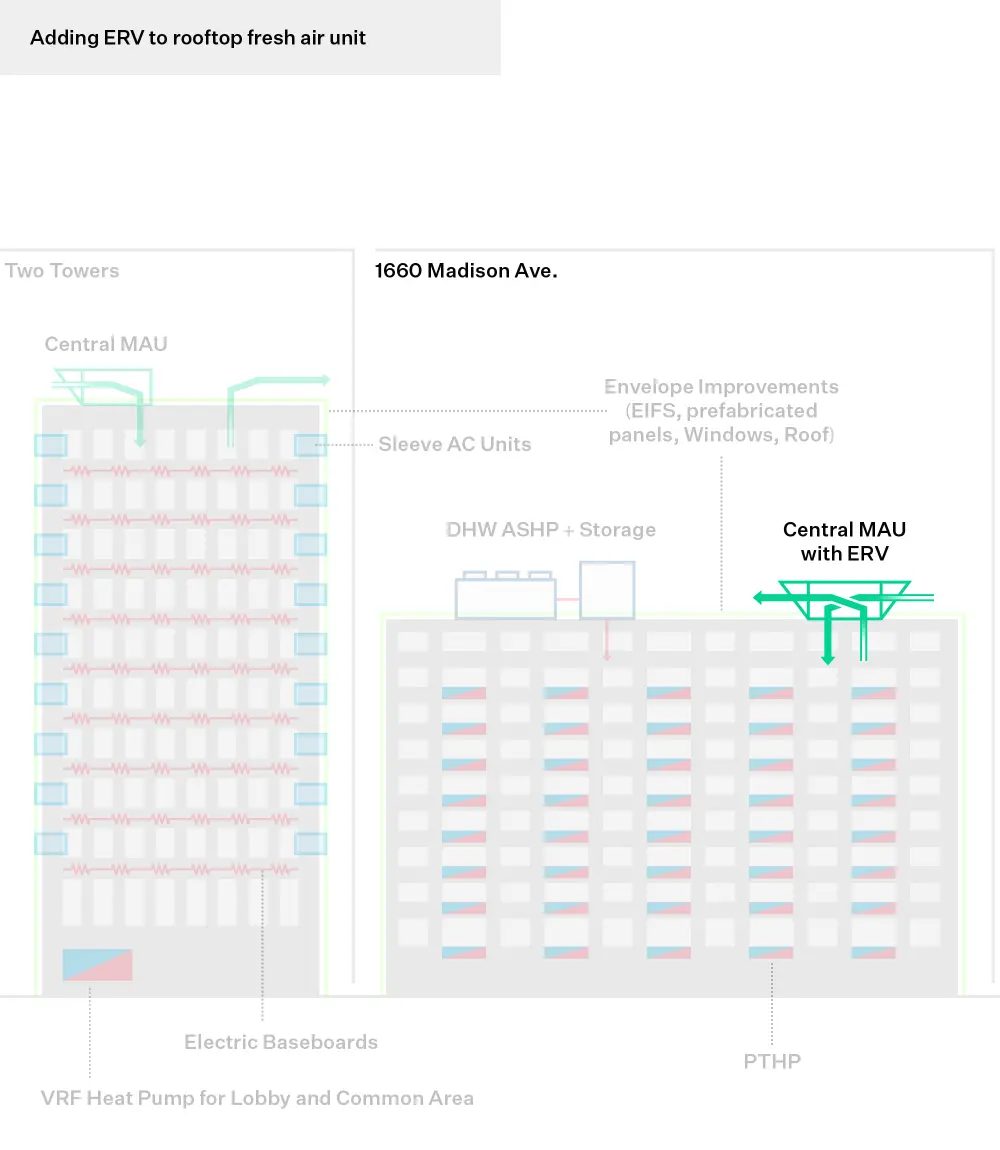
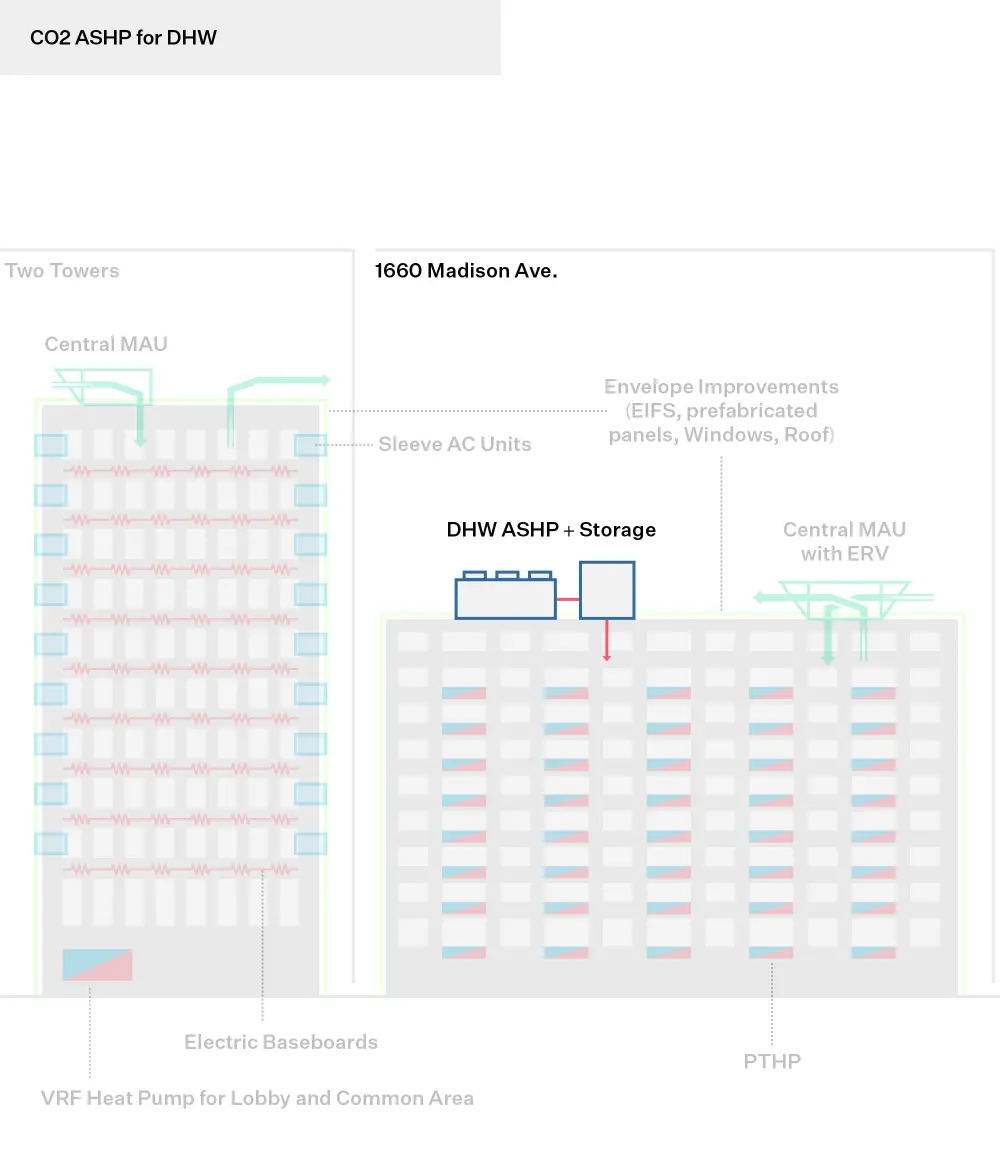
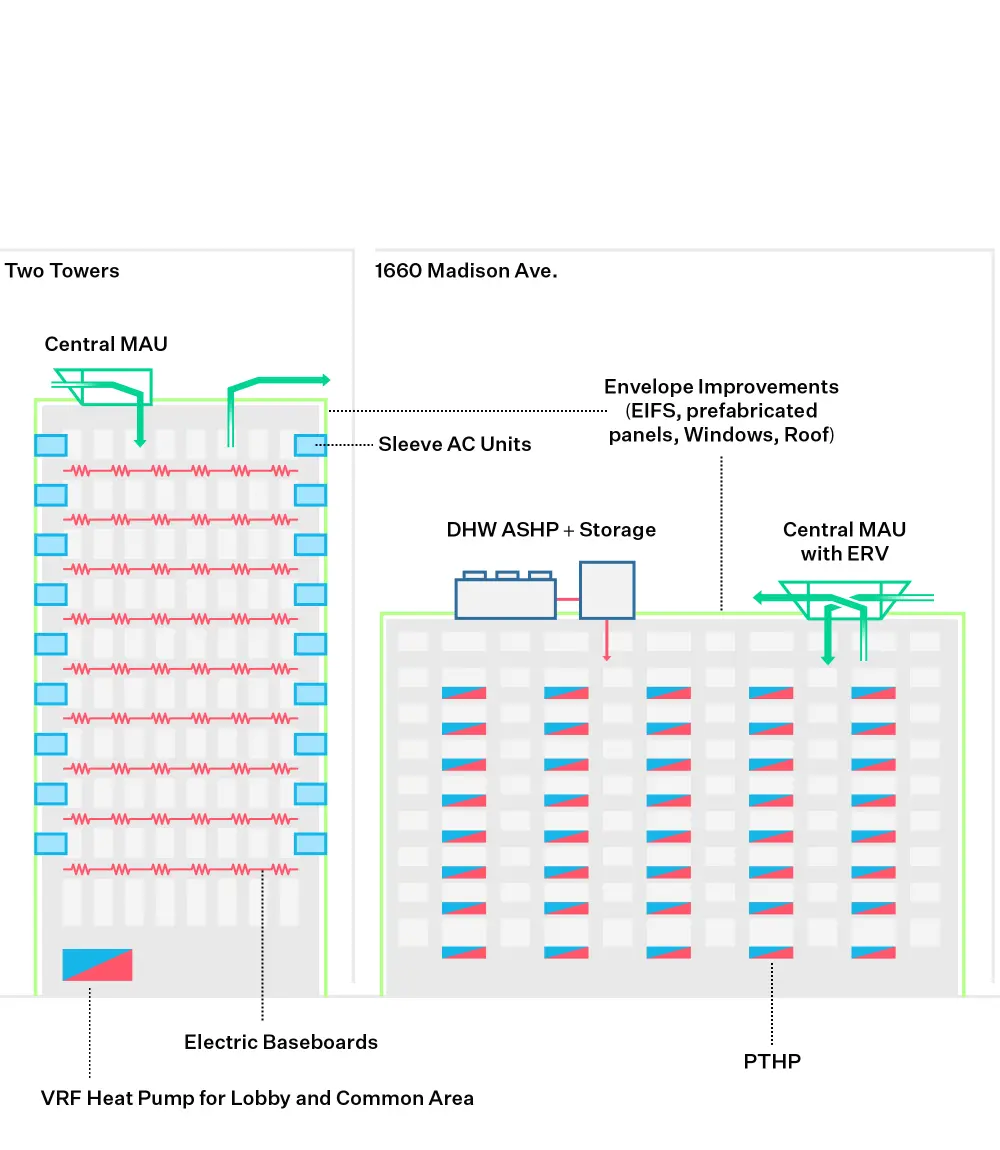
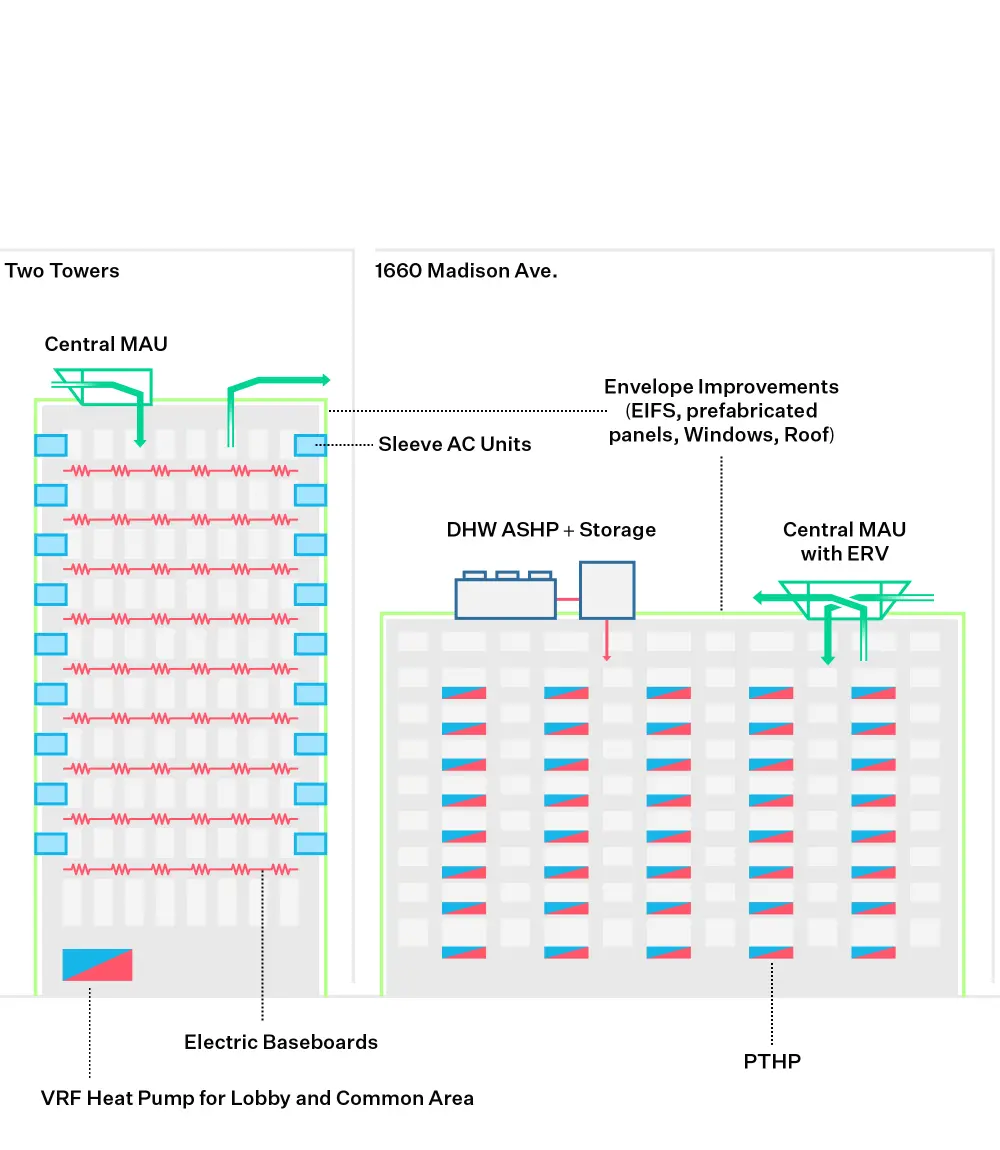
Reduce Energy Load
Re-cladding of the 3 buildings is estimated to avoid $10 million of LL11 compliance costs between now and 2046. One portion of the project is using prefabricated external wall panels from Dextall to minimize installation time and therefore tenant disruption.
- Envelope Improvement: Install exterior wall and roof insulation (EIFS overclad and panelized wall system with integrated high performance windows, dependent on location, and commercial window replacement)
- Submetering
Recover Wasted Heat
- Energy Recovery Ventilator (ERV): install ERV unit into exhaust risers to recapture exhaust heat and preheat fresh air
Partial Electrification
Replacing apartment electric resistance heating baseboards and sleeve air conditioning units with modular Packaged Terminal Heat Pumps (PTHP), and installing CO2-based heat pumps for Domestic Hot Water (DHW) production will significantly increase system efficiency and reduce energy use
and costs. The PTHP installation work is coordinated with the panelized exterior wall system to integrate necessary electrical upgrades and condensate lines and minimize installation time as a result.
- Heat Pumps: Replace electric baseboard heating with Package Terminal Heat Pumps (PTHPs) for apartments and install VRF system for common areas
- Domestic Hot Water: CO 2 Air Source Heat Pump (ASHP) for DHW production
- Laundry appliance
Step 3
Step 3: Build the Business Case
Making a business case for strategic decarbonization requires thinking beyond a traditional energy audit approach or simple payback analysis. It assesses business-as-usual costs and risks against the costs and added value of phased decarbonization investments in the long-term.
Strategic Decarbonization Action Plan
An emissions decarbonization roadmap helps building owners visualize their future emissions reductions by outlining the CO2 reductions from selected energy conservation measures. This roadmap is designed with a phased approach, considering a 20- or 30-year timeline, and incorporates the evolving benefits of grid decarbonization, ensuring a comprehensive view of long-term environmental impact.
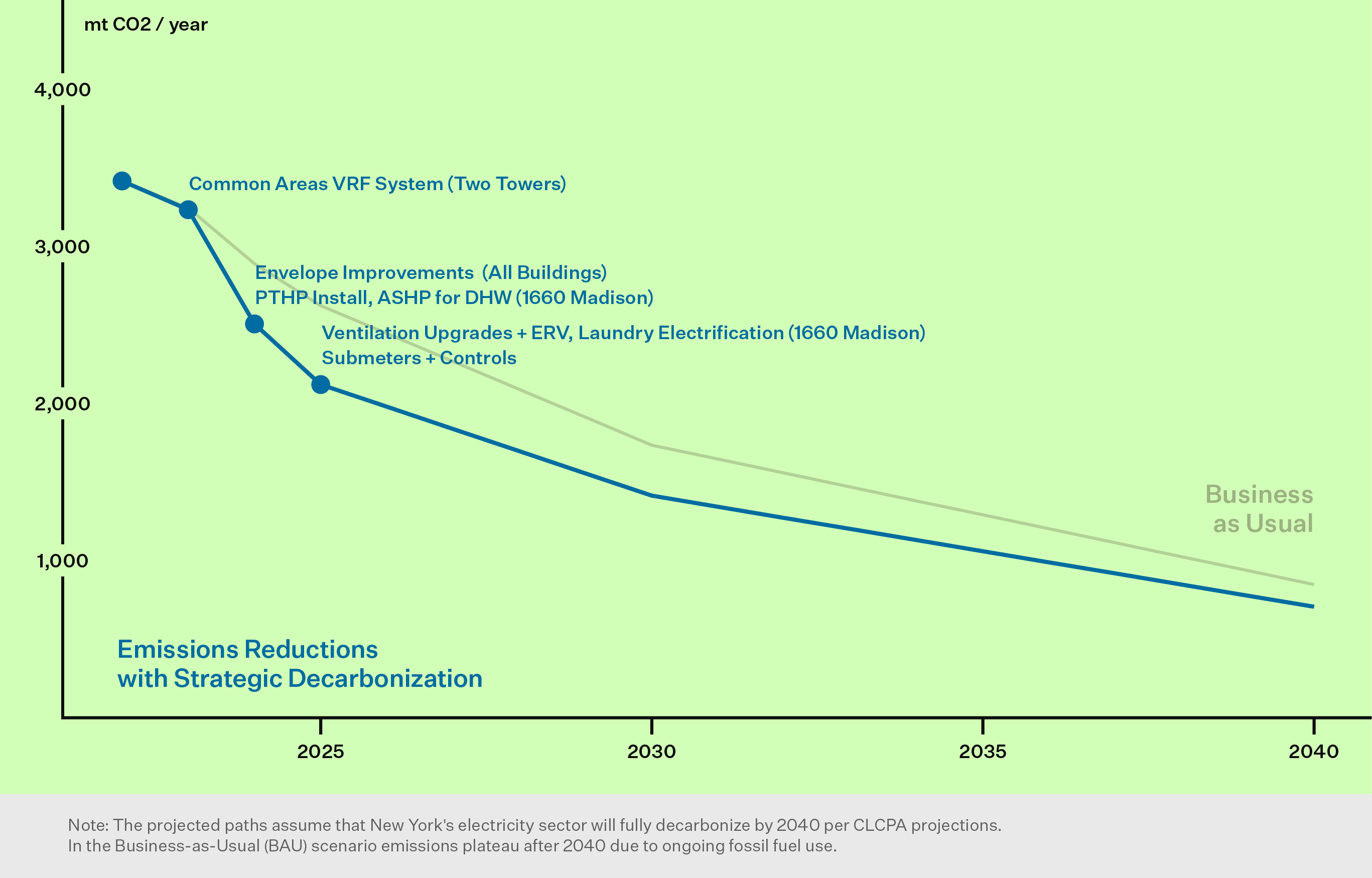
In 2020, L+M envisioned a deep retrofit plan for the Heritage and formed its consulting team including Inglese and Cosentini. L+M and SWA discussed the possibility of applying to the Empire Building Challenge initial round to further study possibilities for the building and to support the retrofit plan. In 2021 the L+M was awarded the next round of funding to execute the vision. The process encouraged the team to think holistically about the project and identify as many opportunities as possible to eliminate fossil fuel usage, reuse waste heat, and reduce loads on the building.
Throughout 2022 to the present, the team has met regularly to review each aspect of the design, review submittals and recommend improvements, and review construction schedules and decision-making deadlines to ensure all elements of the project are completed as needed.
As a socially responsible developer, sustainability is central to L+M’s mission to create green, high-quality affordable housing. Since many of our projects are income-restricted, L+M is focused on reducing operating costs to allow for greater affordability.
Partnering with NYSERDA on developing a roadmap to carbon neutrality will benefit our investors, residents, our communities, and our environment, both now and in the future
L+M hopes to use the Empire Building Challenge as a chance to pilot new technologies and create a scalable approach to reducing emissions throughout its portfolio.
Furthermore, L+M is committed to transparency and sharing retrofit project economics and case studies with the broader industry. L+M’s pre-construction, engineering, and development teams actively share best practices with industry peers through the New York State Association for Affordable Housing (NYSAFAH), The Urban Land Institute (ULI) and other industry organizations.
L+M is also an active participant in conferences and stakeholder sessions with NYSERDA and is committed to working with state and local governments, equipment suppliers, contractors, and the broader real estate industry to decarbonize the built environment.